Im Laufe des technischen Fortschritts und der größeren Komplexität der technischen Lösungen werden immer höhere Anforderungen an die Maschinen- und Anlagenteilen gestellt, die perfekt an andere Teile angepasst werden müssen, so dass das Ganze effektiv und mit maximaler Leistung funktioniert. Deswegen tolerieren die gegenwärtigen Fahrzeuge das kleinste Spiel oder die geringsten Abweichungen von der Maßnorm nicht.
Wie soll man die Anforderungen der OEM Kunden – denke die Fahrzeugnutzer sicherstellen und den Teil liefern, der effektiv ist und ohne übermäßige Verschleißbarkeit arbeiten wird?
Dazu sind die hochleistungsfähige und qualitative Bearbeitung und die hochqualitativen Messgeräte unerlässlich, die den ganzen Prozess kontrollieren lassen. Die neusten Kontrollmesssysteme lassen die kleinsten Abweichungen entdecken, wodurch man die Korrektur vornehmen und die Verluste eliminieren kann.
Wie funktioniert das neuartige Qualitätskontrollsystem?
Früher wenn man über Qualitätskontrolle gedacht hat, hatte man das Bild des einsamen Qualitätsprüfers vor den Augen, der ein Teil nach dem anderen augenscheinlich überprüft und die fehlerhaften Teile zur Seite ablegt. Gegenwärtige Einstellung zu den Vermessungen hat sich komplett geändert.
Im Falle der Koordinatenvermessung vermessen wir nicht den Abstand vom Punkt A bis zum Punkt B, aber die Koordinatenwerte X, Y, Z der einzelnen Punkte auf der Oberfläche des gemessenen Objekts. In den meisten klassischen Vermessungsanlagen verläuft die Vermassung nach dem kartesischen Koordinatensystem, d.h. die beweglichen Vermessungsgruppen bewegen sich in drei gegenseitig zu diesen Gruppen senkrechten Richtungen. Das Arbeitsteil an der Anlage ist der Vermessungskopf, demnächst wird die Vermessung derer Lage durch die Messlineale durchgeführt, die sich in jeder Anlageachse befinden oder durch die Encoders am Vermessungskopf (im Falle der 5-Achsen Systemen). Anhand der registrierten Koordinaten der einzelnen Vermessungspunkten bezeichnet das PC die geometrischen Figuren, aus denen der gemessene Teil besteht. Die Eigenschaften dieser Figuren sind die Maße, die Entfernungen der einzelnen Vermessungspunkte von definierten Bezugspunkten sind die Gestaltabweichungen.
Schema der Ablesung von Messpunkt – angebrachte Zeichnung Vermessungsanlage DEA Global Silver Performance – Quelle mechanik.media.pl
Typen der Vermessungsköpfe
Impuls – Umschalt- Kopf – der Impuls verursacht „das Ablesen” der Punktkoordinaten vom Maschinensystem, die auf einzelnen Achsen montiert sind und wirkt auf die Antriebe und die Anlagesteuerung.
Impulskopfstücke PH20 i PH10 – Quelle renishaw.pl
Der Scankopf, der in der passiven und aktiven Version vermisst (der sich durch die Art und Weise der Anbringung des Vermessungsdruckes unterscheidet). Der Scankopf ermöglicht nicht nur das Entdecken des Kontaktpunktes der Vermessungsendung mit der Oberfläche des gemessenen Gegenstandes aber auch die Bestimmung der Koordinatenwerte dank der Vermessungswandlern, die in jeder Achse vorkommen. Dank diesem Zustand vermisst der Kopf die Lage der Endung in den Koordinaten X, Y, Z mit der Bildauflösung von 0,1µm. Bei der Vermessung wird der umgewandelte Signalwert von Wandlern zum Koordinatenwert der Kopflage addiert, die durch Steuerung registriert sind. Dadurch ist es möglich, die z.B. die Karte der Abweichungen der Gestaltformen zu bestimmen.
Scankopf REVO-2 – Quelle renishaw.com
Kontaktfreies Kopfstück – angewendet bei Gegenständen, die aus weichen Materialien bestehen und bei einigen Metallgegenständen, die kleinerer Vermessungspräzision erfordern. In solch einem Fall erfolgt die Lokalisierung des Vermessungspunktes mittels Lasertriangulationskopfstücke oder durch die Bildanalyse der Oberfläche vom CCD-Kopf. Für die Trangulatiosköpfe ist die Grundlage zur Berechnung der Messflächelage das System der rechtseckigen Dreiecke. Die Diode emittiert das Laserlichtbündel, das nach dem Formen durch das optische System zur Oberfläche des gemessenen Gegenstands läuft. Auf seiner Oberfläche entsteht der Fleck mit dem Durchmesser von mehrzehnten bis mehrhunderten µm. Das Bild des Fleckes wird durch das optische System in der Fotolineal abgebildet.
Zusammenfassung
Es ist unbestritten, dass in der Automobilindustrie die Vermessung auf den Vermessungsanlagen notwendig ist. Zum Glück ist die Auswahl der zuständigen Lieferanten sehr groß und die Auswahl der Vermessungsmethode und der Maschine hängt von den Bedürfnissen der ausgeführten Vermessungen, der Größe der hergestellten Teile und der geforderten Messgenauigkeit – z.B. für die Mehrheit der Präzisionsteile für die Antriebsysteme oder für die Aufhängung ist es schwierig die kontaktfreien Kopfe anzuwenden, die meistens nicht genug genau sind.
Sichtbar ist der Trend, dass häufiger die Scanköpfe statt der Impulsköpfe angewendet werden. Die Entwicklung der Scanköpfe lässt in vielen Fällen die genaueren Vermessungen durch die Anzahl der gesammelten Punkte in der vergleichbaren und sogar kürzer Zeit zu erreichen und in langer Zeitperspektive scheint es eine wirtschaftliche Lösung zu sein, obwohl am Anfang die Investition teurer ist.
Es zeigt sich oft, dass die Vermessung ein „Engpass” im Herstellungsprozess ist, deswegen ist das 5-Achsen System eine interessante Alternative für die klassischen Vermessungssysteme auf den Koordinatenmaschinen. Ein Beispiel aus unserer Erfahrungen – dank der Anwendung des 5-Achsen Systems konnten wir die Vermessungszeit eines Teils um 54% verringern, was uns der Vorteil in Form der zusätzlichen Vorräte im Bereich der Vermessungen gebracht hat.
Der Umfang der Fragen, die mit der Vermessung der Teile zusammenhängen, ist sehr breit – ich hoffe, dass diese allgemeine Beschreibung der gegenwärtigen Vermessungsmethoden eine Einleitung zur Vertiefung in diese Thematik für die interessierten Personen ist.
Jarosław Kondys
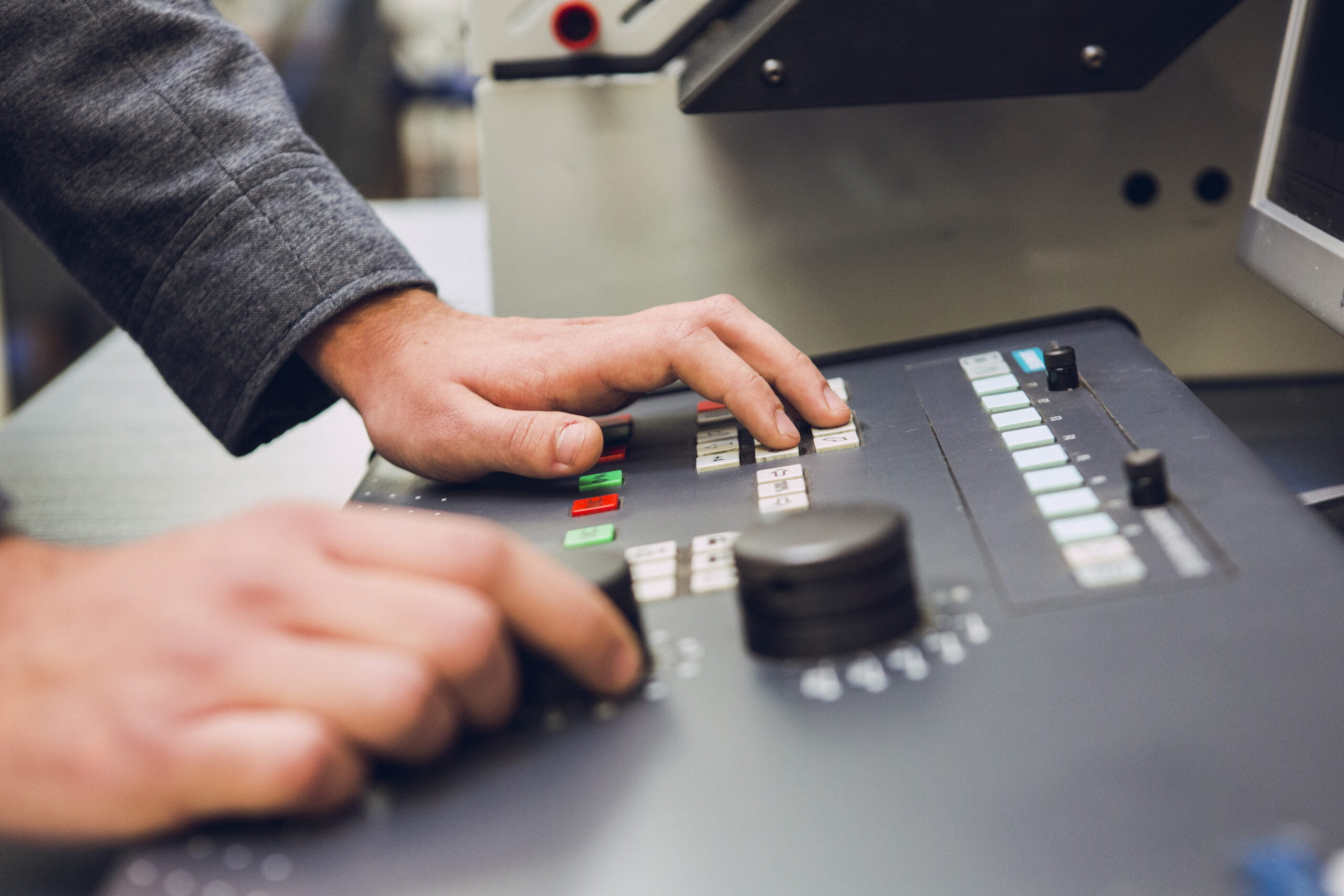