Numerous industries can thrive thanks to the regular supply of metal components. They are parts of furniture, electronic devices, vehicles, and many other commonly available goods. The efficient operation of CNC machines determines whether it is possible to fulfill orders on time and produce details with appropriate precision. Unfortunately, however, even such technologically advanced equipment as CNC machine tools are not failure-free. The production manager, who makes sure that everything is buttoned up to the last button, must know what causes any failures and how to deal with them. Let’s take a closer look at this issue.
CNC machining – what breaks down most often?
CNC machining is a process largely based on modern software that the machine operator uses to give commands to the tools. It would seem, therefore, that a frequent problem will be a failure of the control system, but in fact it is not the cause of most of the faults. As in the case of many other devices operating at high speed, machine tools most often suffer from mechanical injuries caused by intensive use. Mechanisms and tools that take part in production processes every day will wear out and it is natural. It does not mean, however, that one should not be prepared for such an eventuality, especially as the precision and safety of machining processes will depend on ensuring the efficiency and continuity of work.
How to deal with a failure of a CNC machine tool?
A CNC machine that is supposed to work well and not fail, should first of all be properly installed at the workplace. Be especially careful during transport and assembly. Correct leveling and a stable position will help to prevent vibrations in the machining process, which could make it impossible to obtain the desired shapes. In addition, appropriate conditions must be provided for a CNC machine tool so that the device can remain viable for a long time. It needs regular servicing, inspection and replacement of excessively worn out elements. In addition, you should ensure optimal temperature and cooling during operation and not forget about regular lubrication. What else is important? Proper training of employees operating the machine tool. Knowledge of the programming language is crucial here, but it is also worth remembering about health and safety training and familiarizing the staff with safety procedures, so that not only the machine, but also the human being, will not suffer during the intense work.
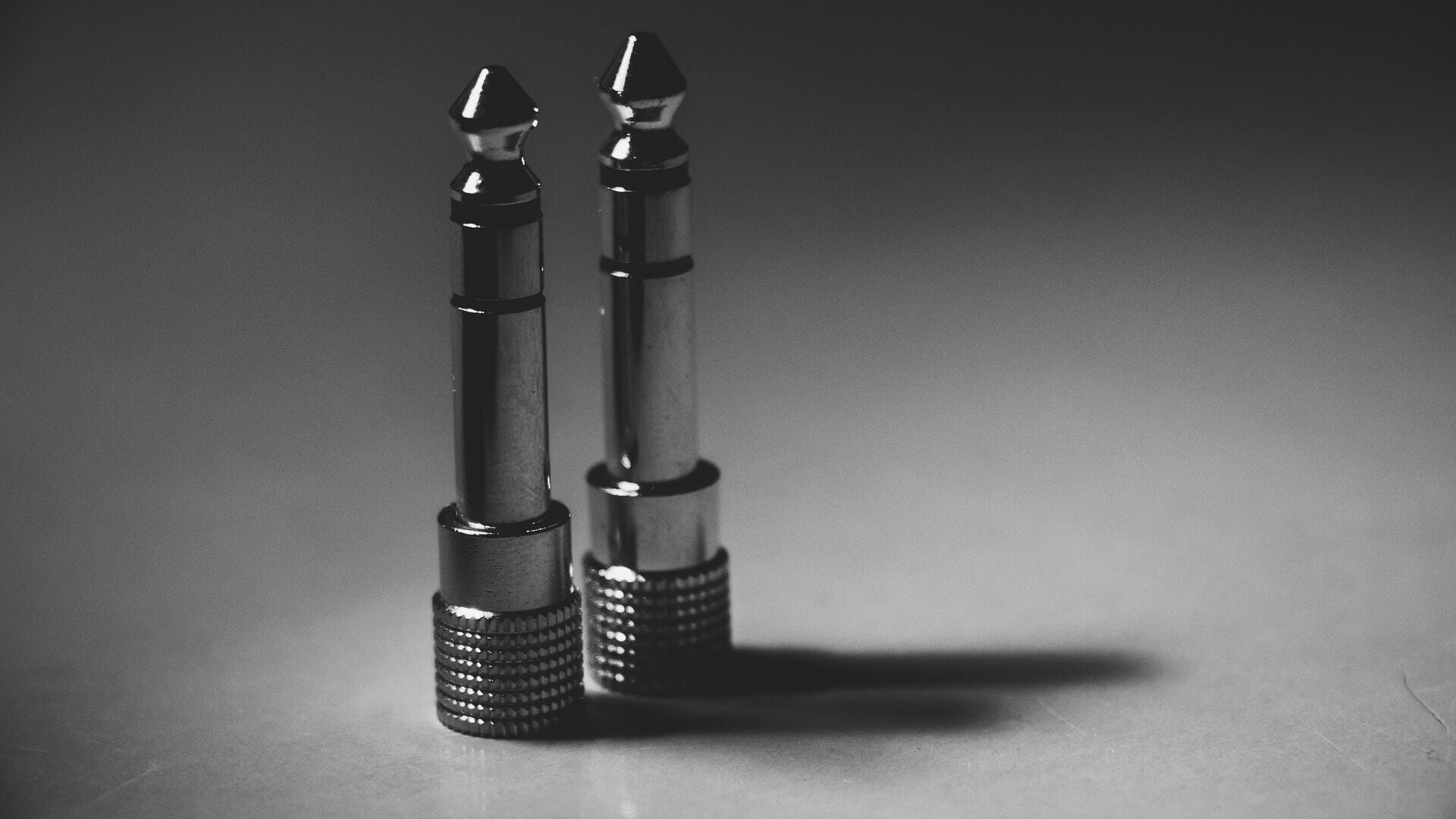