W dobie postępu technicznego i coraz większego skomplikowania rozwiązań technicznych stawia się coraz większe wymagania częściom maszyn i urządzeń, które muszą być perfekcyjnie dopasowanie do innych elementów, aby całość działała sprawnie i z maksymalną wydajnością. Dlatego współcześnie produkowane samochody, nie tolerują najmniejszych luzów czy odchyleń od wymiarowej normy.
Jak zapewnić spełnienie wymagań klienta, OEM a w domyśle użytkownika samochodu, i dostarczyć część, która będzie pracować sprawnie i bez nadmiernego zużycia?
Niezbędna do tego jest wysokowydajna obróbka w wysokiej jakości i urządzenia pomiarowe, które pozwalają na nadzorowanie tego procesu. Nowoczesne systemy kontrolno-pomiarowe mogą wychwycić takie ułamkowe odchylenia, dzięki czemu można dokonać korekty i wyeliminować straty.
Jak funkcjonuje nowoczesny system kontroli jakości?
Dawniej gdy myślało się o kontroli jakości, często nasuwał się obraz samotnego pracownika, który sztuka po sztuce ogląda każdy detal i odrzuca na bok te wadliwe. Obecnie podejście do pomiarów zupełnie się zmieniło.
W przypadku pomiarów współrzędnościowych nie mierzymy odległości z punktu A do punktu B, lecz wartości współrzędnych X, Y, Z pojedynczych punktów na powierzchni mierzonego przedmiotu. W większości klasycznych maszyn pomiarowych pomiar odbywa się w układzie współrzędnych kartezjańskich, tzn. ruchome zespoły pomiarowe maszyny przemieszczają się w trzech wzajemnie prostopadłych kierunkach. Organem roboczym maszyny jest głowica pomiarowa, natomiast pomiar ich położenia realizują liniały pomiarowe znajdujące się w każdej z osi maszyny lub enkodery w głowicy pomiarowej (w przypadku systemów 5-osiowych). Na podstawie zarejestrowanych współrzędnych poszczególnych punktów pomiarowych komputer maszyny wyznacza figury geometryczne, z których składa się element mierzony. Cechy tych figur są wymiarami, a odległości poszczególnych punktów pomiarowych od zdefiniowanych elementów odniesienia to odchyłki kształtu.
Schemat odczytu punktu pomiarowego – wykorzystano ilustrację Maszyna pomiarowa DEA Global Silver Performance – źródło mechanik.media.pl
Typy głowic pomiarowych
Impulsowa – głowica przełączająca – impuls powoduje “odczytanie” współrzędnych punktu z układów pomiarowych maszyny, zamontowanych na poszczególnych jej osiach oraz oddziałuje na napędy i sterowanie maszyną.
Głowice impulsowe PH20 i PH10 – źródło renishaw.pl
Skanująca – głowica mierząca w wersjach pasywnej i aktywnej (różniąca się sposobem zadawania nacisku pomiarowego). Głowica skaningowa umożliwia nie tylko wykrycie styku końcówki pomiarowej z powierzchnią mierzonego przedmiotu, ale również wyznaczenie wartości współrzędnych dzięki przetwornikom pomiarowym występującym w każdej z osi. Dzięki temu stanowi głowica mierzy położenie końcówki we współrzędnych X, Y, Z z rozdzielczością 0,1µm. Podczas pomiaru przetworzona wartość sygnału z przetworników jest dodawana do wartości współrzędnych położenia głowicy zarejestrowanych przez sterownik, dzięki czemu możliwe jest np. wyznaczenie mapy odchyłek błędów kształtu.
Głowica skanująca REVO-2 – źródło renishaw.com
Bezstykowa – stosowane w przypadku przedmiotów wykonanych z miękkich materiałów oraz niektórych elementów metalowych wymagających mniejszej precyzji pomiaru. W ich przypadku lokalizacja punktu pomiarowego odbywa się za pomocą laserowych głowic triangulacyjnych lub poprzez analizę obrazu powierzchni z głowicy z kamerą CCD. Dla głowic triangulacyjnych podstawą wyliczenia położenia powierzchni pomiarowej jest układ trójkątów prostokątnych. Dioda laserowa emituje pomiarową wiązkę światła, która po uformowaniu przez układ optyczny biegnie w kierunku powierzchni mierzonego przedmiotu. Na jego powierzchni tworzy się plamka o średnicy od kilkudziesięciu do kilkuset µm. Obraz plamki jest odtwarzany poprzez układ optyczny na fotolinijce, gdzie następuje odczyt wartości.
Podsumowanie
Nie ulega wątpliwości, że w przemyśle motoryzacyjnym pomiar na maszynach pomiarowych staje się koniecznością. Na szczęście wybór dostawców takich maszyn jest szeroki, a dobór metody pomiarowej i maszyny zależy głównie od potrzeb wykonywanych pomiarów, wielkości wykonywanych części i wymaganej dokładności pomiarów – np. do większości precyzyjnych części do układów napędowych lub zawieszenia ciężko zastosować głowice bezstykowe które z najczęściej mają zbyt małą dokładność.
Zauważalnym trendem jest stosowanie głowic skanujących kosztem głowic impulsowych. Rozwój głowic skanujących w wielu przypadkach pozwala na osiągnięcie dokładniejszych pomiarów poprzez ilość zbieranych punktów w porównywalnym, a czasem nawet krótszym czasie i w dłuższej perspektywie czasu wydaje się rozwiązaniem ekonomiczniejszym pomimo początkowo wyższej ceny inwestycji.
Pomiar często okazuje się „wąskim gardłem” w procesie wytwarzania, dlatego ciekawą alternatywą dla klasycznych układów pomiarowych na maszynach współrzędnościowych jest system 5-cio osiowy. Na przykładzie naszych doświadczeń dzięki zastosowaniu układu 5-cio osiowego potrafiliśmy ograniczyć czas pomiaru pojedynczej części o 54% co dało wymierne korzyści w postaci dodatkowych rezerw w obszarze pomiarów.
Zakres zagadnień związanych z pomiarem części jest bardzo obszerny – mam nadzieję, że ogólny zarys współczesnych metod pomiarowych może stać się wstępem do zagłębienia się w tą tematykę dla osób zainteresowanych.
Jarosław Kondys
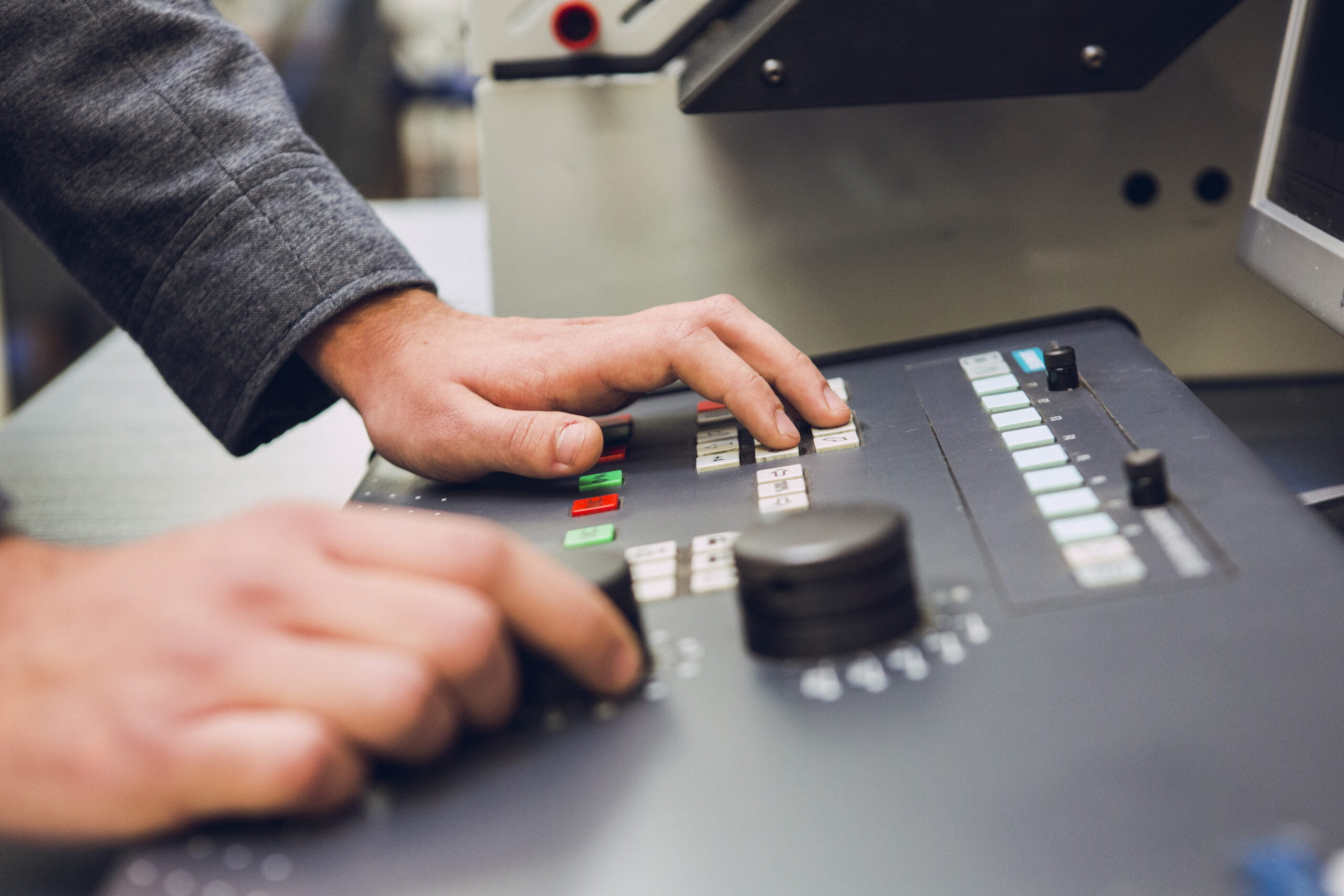