Lean Management im CNC-Zerspanen findet immer häufiger nicht nur in großen Konzernen sondern auch in kleinen Familienfirmen Anwendung. Der Grund dafür ist, dass gute Lösungen und Arbeitsstandards mit sich große Ersparnisse bringen ohne viel dafür zu zahlen Dzieje się tak, ponieważ dobre rozwiązania i standardy pracy przynoszą spore oszczędności małym kosztem. Es zählt das Ergebnis, deswegen sollte man überlegen, ob wir über SMED, KAIZEN, 5S, TPM sprechen wollen oder einfach über schnelle Umrüstungen, über gute, kostenfreie Verbesserungsideen für die Organisation der Arbeitsstände oder alle wichtigen Tätigkeiten, die mit der Instandhaltung und Bedienung der Maschinen verbunden sind. Einfacher oder?
Nach der Lektüre des letzten Artikels wissen wir bereit, dass es am wichtigsten ist, sich auf dem Mehrwert zu konzentrieren und alle möglichen Verluste zu eliminieren. Wie viele verschiedene Fertigungen, Technologien es gibt, so unterschiedliche Zugänge und Einführungsmethoden von LEAN wird es geben. Wie sieht es genau in der Zerspanungswelt aus?
Erstens – was ist unser grundlegender Mehrwert? Nach der einfacher Definition ist es das, wofür der Kunde bezahlen will, dann lautet die Antwort der bearbeitete Teil. Also die wichtigste Zeit ist die Zerspanungszeit. Habt ihr jemals überlegt, wie viel Prozent von der ganzen zugänglichen Zeit im Jahr nur die Zerspanungszeit in Anspruch nimmt*? 60%? Das wäre super. Vielleicht 35%? Ganz nah. Die Antwort zwingt uns zum Überlegen. Statistisch NUR 24% ist die Zeit des Mehrwertes. Wie ist das möglich? Wenn man berücksichtigt, dass wir im Jahr 8760 Stunden zur Verfügung haben, 60% ist die Zeit der Produktion. In dieser Zeit außer Maschinenzeit, die 50 % beträgt, verbergen sich auch die Umrüstungen, die Störungen, die Teilaustausche und die Stillstände, die die verlorene Zeit sind. Wenn wir weiter schauen, in der Maschinenzeit haben wir nicht nur mit der Zerspanung zu tun – Werkzeugaustausch, Positionieren – das ist auch verlorene Zeit. Zusammenfassend die Multiplikation der Zeit, die mit der Produktion zusammenhängt, Maschinenzeit und Zerspanungszeit beträgt 24%.
Beschreibung der Zeichnung:
8760 zugängliche Stunden im Jahr
60% die geplante Produktionszeit
40% die Zeit, die nicht mit der Produktion verbunden ist
50% Maschinenzeit
25% Umrüstung, Stillstand
10% Änderung des Objektes
10 % Störungen
5% andere
Zeichnung Nr.. 1. Zeitverteilung des Mehrwertes in der Zerspanung (eigene Bearbeitung, die statistischen Angaben von der Firma Sandvik Coromant)
Zweitens – die Auswahl der Methode, die wesentlich die Zeit verkürzt, die kein Mehrwert ist. Ich empfehle SMED – Single Minute Exchange of Die. Eine Zerspanungsmaschine – viele Verfahren – wir streben nach der Zeitreduktion, die mit der Umrüstung zur einstelligen Minutenzeit zusammenhängt. Die Umrüstung ist die Zeit, die zwischen dem letzten guten Teil von der vorherigen Produktion und dem ersten guten Teil von der neuen Produktion verläuft. Historisch gesehen ist die erste notierte Probe mit der Anwendung der SMED Methodologie in Japan in der Schiffbauindustrie von Toyota gelungen, dabei hat man die Umrüstungszeit der 1000-Tonen Presse von 4 Stunden auf 3 Minuten reduziert! Gut, aber womit soll man starten? In der ersten Phase sollen alle Tätigkeiten in interne und externe geteilt werden. Die Tätigkeiten, die man nur bei der ausgeschalteten Maschine ausführen kann, nennen wir die internen und andere bezeichnen wir als externe. Wenn die Teilung gemacht wurde, versuchen wir in der zweiten Phase die internen Tätigkeiten in die externen umzuwandeln und alle unnötigen Tätigkeiten eliminieren. Die letzte Phase ist die Verbesserung aller Tätigkeiten, die zur Umrüstung gehören und das Erstellen des Plans für gegebene Umrüstung. Zum Beispiel bevor die Maschine ausgeschaltet wird, ist es gut alle Werkzeuge zu messen, die zur Zerspanung des Teils der neuen Produktion notwendig sind. Ich empfehle auch sich mit neuen Technologien der Befestigungen auseinanderzusetzen wie z.B. „zero-point clamping system” dieses System lässt schnelle Umrüstung mit der Wiederholbarkeit des Positionierens von 2,5 Mikrometer zu**.
Der letzte wichtige Faktor, der direkt die Mehrwertzeit beeinflusst, ist der Zustand der Zerspanungsmaschine. Wir können kurze Umrüstungen, gut organisierte Arbeitsstände, gut durchgedachten Prozess haben, aber wenn die Störung vorkommt, verlieren wir alles. Ein paar Worte über TPM-ie – aus Englischem Total Productive Maintenance also Totale Produktionsbetriebsinstandhaltung. Das Hauptziel ist die Sicherstellung des guten technischen Zustands der Maschinen. Wann wissen wir, dass TPM gut in der Firma implementiert ist? Erstens wir „löschen keine Brände” mehr und wir beugen sie vor, zweitens sprechen wir über kollektives Bewusstsein – es gibt keinen Begriff wie „ich produziere, du reparierst ” – für TPM ist das ganze Team verantwortlich. Es gibt acht Pfeiler, über die ich empfehle in der Freizeit zu lesen, ich will mich jedoch auf die Verluste in TPM konzentrieren, also:
- Störungen
- Umrüstungen
- Mikrostillstände
- Reduzierte Geschwindigkeit
- Schrott
- Inbetriebnahme
Punkt 1 u. 2 beziehen sich auf die Verluste der Zugänglichkeit – alle geplante und nicht geplante Stillstände, Werkzeugaustausche als auch die Frühstückspausen gehören zu dieser Gruppe.
Punkt 3 u. 4 sind die Nutzungsverluste. Der Punkt über reduzierte Geschwindigkeit ist interessant. Es ist die Wahrheit, dass es besser ist, wenn die Maschine mit der größten Geschwindigkeit arbeitet als wenn man sie künstlich verlangsamt. Nach den Übungen an der Uni aus TPM habe ich einen Satz des Professoren „Maschine soll arbeiten“ in Erinnerung. Die letzten zwei Punkte beziehen sich auf die Qualitätsverluste – alle NOKs, Störungen, Verbesserungen zählen zu dieser Gruppe.
Hilfreich werden die Anzeiger zur Bestimmung der Effektivität der Maschinenpark sein. Der wichtigste Anzeiger ist OEE – es ist das Produkt aus Zugänglichkeit, Auslastung und Qualität. Die nächsten zwei sind MTBF (Mean Time Between Failures), also Durchschnittszeit zwischen den Störungen und MTTR (Mean Time to Repair), also der durchschnittliche Reparaturzeit.
Es gibt viele Methoden in LEAN, alle auf einmal einzuführen, ist nicht möglich und nicht vernünftig. So wie ich erwähnt habe, soll man überlegen, was bei der konkreten Produktion hilfreich wäre und dann den ersten Schritt zu machen. Ich wünsche gute und kluge Verbesserungsmaßnahmen.
Natalia Matuszczyk
*Anmerkung – Angaben für einheitlichen und Kleinserienverfahren. In vollautomatisierten Massenverfahren kann der Anteil der Produktions- und Zerspanungszeit 60 % betragen.
** https://www.zeroclamp.com/en/zero-point-clamping-system/
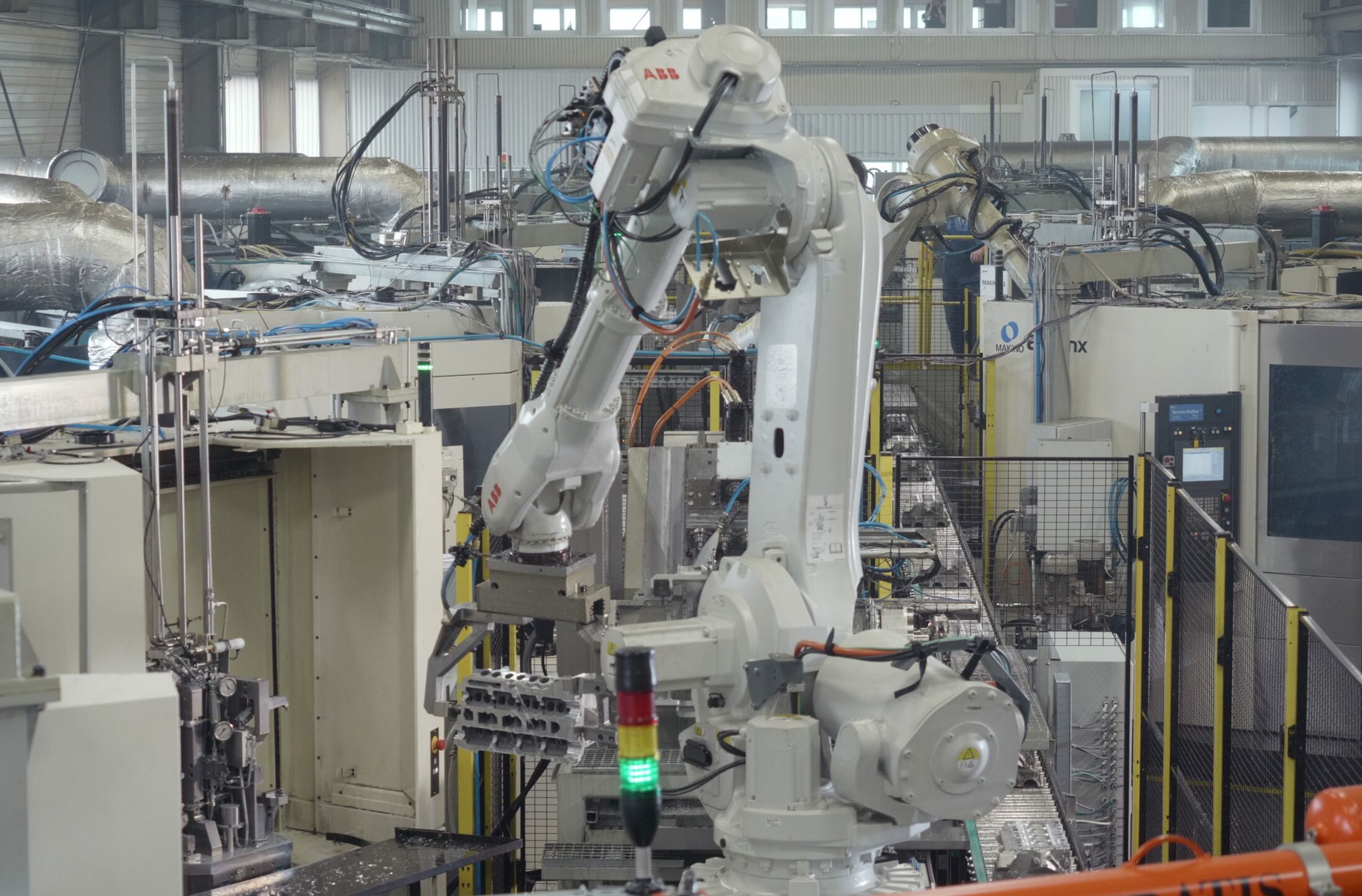