Lean Management in CNC machining is increasingly used not only in large corporations but also in small family businesses. This is because good solutions and work standards bring considerable savings at a low cost. The effect counts, so it is worth considering whether we want to talk about SMED, KAIZEN, 5S, TPM or simply and straightforwardly about quick changeovers, good cost-free ideas for improvement, organization of workstations and all important activities related to the maintenance and operation of machines. Easier, right?
After having read the previous article, we know that the most important thing is to focus on added value and eliminate as much waste as possible. The more different types of production and technologies the more various approaches and methods of LEAN implementation. How does it exactly work in the machining world?
First of all – what is our core added value. Looking at a simple definition, that is ‘what the customer wants to pay for’, the answer is the processed detail. So the most important time is the cutting time. Have you ever wondered how many percent of all available time in a year is purely machining time*? 60%? Would be great. Maybe 35%? Close. The answer gives much food for thought. Statistically, ONLY 24% is value added time. How is that possible? Considering that we have 8760 hours available a year, 60% is production time. During this time, apart from the machine time, which is 50%, there are also hidden changeovers, breakdowns, workpiece replacements and stoppages, which are all wasted time. Going further in machine time, we do not have machining itself – tool change, positioning are also wasted time. Summing up, the ratio of production time, machine time and cutting time is 24%.
Fig. 1. Time distribution of value added in machining (own elaboration, statistical data from Sandvik Coromant)
Secondly – choosing a method that will significantly reduce the time that is not an added value. I recommend SMED – Single Minute Exchange of Die. One machine tool, many processes – we strive to reduce the time associated with set-up to a single-digit number of minutes. Changeover is the time that passes between the last good part of the previous production and the first good detail of the new production. Historically, the first recorded successful attempt to use the SMED methodology took place in Toyota’s shipbuilding industry in Japan, where the changeover time of a 1000 ton press was reduced from 4 hours to 3 minutes! Great, but where to start? In the first phase, all activities should be divided into internal and external. Activities that can be performed only with the turned off machine are called internal activities and the rest are external activities. Once the division is done, in the second phase we try to transform the internal activities into the external ones and try to eliminate all unnecessary tasks. The last phase is the improvement of all the activities that take part in retooling and the development of a plan for a given retooling. For instance, before the machine turn – off, it is good to prepare and measure all the tools needed to process a new production part. I also recommend you to get interested in modern clamping technologies, such as “zero-point clamping system” allowing for very fast retooling with positioning repeatability of 2.5 micrometers **.
The last important factor that directly affects the time added value is the condition of the machine tool. We can have a short changeover time, an organized workplace, a well-thought-out process but when a machine breakdown occurs we lose everything. A few words about TPM – Total Productive Maintenance. The main goal is the care for the technical condition of machines. When is it known that TPM is successfully implemented in the company? Firstly, we stop “extinguishing fires” and we are able to prevent their occurrence and secondly, we talk about collective awareness – there is no concept of “I produce and you repair” – the entire crew is responsible for TPM. There are eight pillars that I recommend reading about in your spare time, while I want to focus on TPM losses, that are :
- Failures
- Changeovers
- Minor stoppages
- Reduced speed
- Scrap
- Commissioning
Points 1 and 2 refer to loss of availability – all planned and unplanned stops, tool changes as well as refreshment breaks belong to this group.
Points 3 and 4 are use losses. An interesting point is the reduced speed. It is true that it is better to run the machine at maximum speed than to slow it down on purpose. After the TPM class, I remember exactly teacher’s one short sentence – “The machine has to work”.
The last two points are quality losses – all NOKs, defects, corrections are exactly this group. See: CNC machining in our offer.
Undoubtedly, indicators determining the efficiency of the machine park will be helpful. The most important is OEE and it is nothing more than the ratio of availability, use and quality. The next two are MTBF (Mean Time Between Failures) and MTTR (Mean Time to Repair) namely the average repair time.
There are a lot of methods in LEAN, introducing all of them at once is not only impossible but also unwise. As I mentioned, it is think about what will be helpful in optimizing a specific production and take this first step. I wish you good and wise improvements.
Natalia Matuszczyk
* note – data for a single-unit and small-volume processes. In fully automated mass processes, the percentage of production / machining time can be as high as 60%.
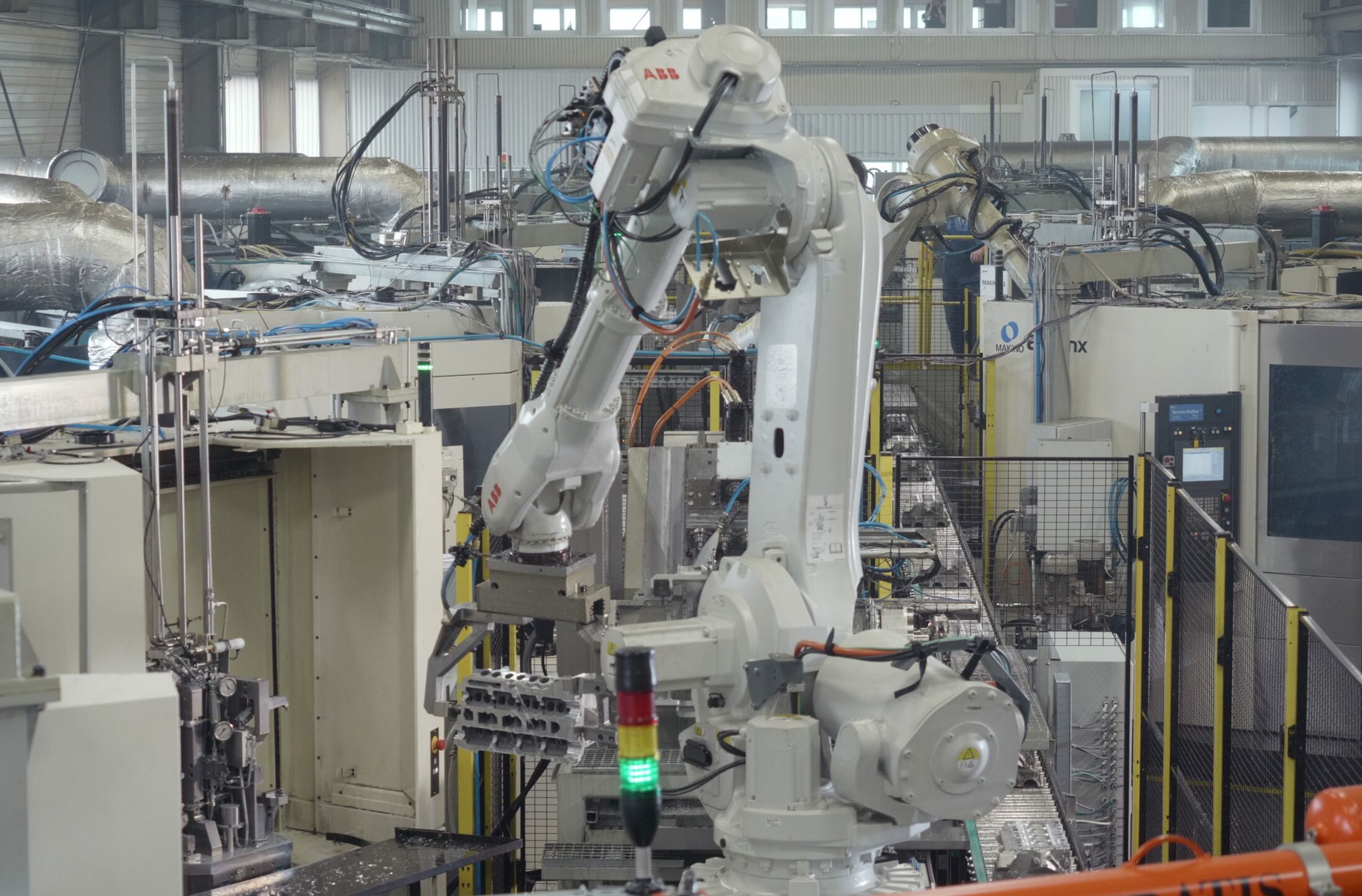