How to produce wisely, that is the question. Continuous optimization is the motto of the Japanese philosophy of Lean Management and western WCM i.e., World Class Manufacturing. The goal is to produce faster, better and cheaper. The aim is to achieve a better quality of workpieces, to eliminate losses and reduce machining time and preparation time. How to achieve zen in machining?
There are many possibilities and usually the simplest method is also the best one. Today I will tell you about a few proven solutions that can be applied in any production.
But let’s start with the basics – what is Lean Manufacturing? It is a lean production based on a smart and clever work. The basis is the continuous improvement and implementation of Deming principle – Plan, Do, Check, Act, i.e., the implementation of actions in four constantly repeated steps. Start by planning the task, then implement a small-scale activity and assess whether you have obtained the intended results. If the effect is satisfactory, it’s time to implement the activity on a large scale, if not – start the process from the beginning focusing on optimization.
What to avoid? 7 great wastes or 7 types of muda (a Japanese word for waste):
- Overproduction
- Inventory
- Unnecessary transport
- Unnecessary motion
- Defects
- Waiting
- Extra Processing
It’s also worth mentioning the eighth muda, the non-utilized potential. In production, there are often valuable employees whose skills and capabilities are not fully used and developed.
We know what to avoid but do we know what is the most important in every production? It is about added value, i.e. activities that directly affect the functional features of the product for which the customer wants to pay.
After a short theoretical introduction, it’s time for some optimization examples.
- 5s and Standardization
It is often said that the easiest way to start is to… clean up! Why? Because the introduction of 5S in production usually does not require financial outlay and the effects can be seen immediately. So what is hidden under the enigmatic acronym 5S? Seiri – Seiton – Seiso – Seiketsu – Shitsuke or Sort, Set in order, Shine, Standardize and Sustain.
First, „Sort” – in this step, it is worth dividing all the items at the workplace into those that we use often and those that we use rarely and assign them a suitable place. Then „Set in order” – a place for everything and everything in its place, i.e. time for good visualization. Colors, tapes, photos, boards , anything that could be useful and facilitate the organization. Third step – „Shine” led by three guidelines – when?/who?/what?. Schedules will be of much help here. Then „Standardize” as one of the most important steps. This is where all the previous steps are brought together. The last step, i.e. „Sustain”, closes 5S. Audits (reviews) are essential to maintain the quality of the developed standards.
- Spaghetti diagram as the way of good positioning of machine tools.
Let’s imagine a simple process – the raw part is in stock. The operator takes the pre-manufactured part and goes across the hall to the first machine. He realizes that he doesn’t have all the tools he needs so he goes to the tool shop. After pre-treatment, he takes the detail for measurement control. It turns out that the machine is busy and the operator has to wait. After the measurement, he takes the detail to the next machine tool located in a different production hall. After the final processing, the detail returns to the measurement control and then the measured part goes to the warehouse ready to be sent to the customer. After this description, it is already known that the entire process can be optimized.
By analyzing all the operator’s movements, a spaghetti diagram can be drawn. It allows the analysis of the distance travelled by the operator and finding the muda.
There are many possibilities to optimize the example described – let me present a few:
- First, limiting the operator’s movement. Preparation of the workstation before processing significantly reduces the time. In this case, the pre-manufactured product should be transported to the position by the warehouse worker and all the tools needed to perform the tasks should be at the workplace beforehand.
- Second – eliminating excessive quality and waiting. The presented operator takes the part after the first treatment to the measurement control. It is worth considering whether this step is necessary – maybe self-control at the workplace is enough?
- Third – the distance between successive machine tools. Relocation of huge machines is not easy, but a well-thought-out and planned change of location can bring huge time savings and, consequently, increase in productivity and money.
Natalia Matuszczyk
In the next part – a detailed look at cutting time in the Lean philosophy, quick changeovers and TPM are the answer to an effective machine park.
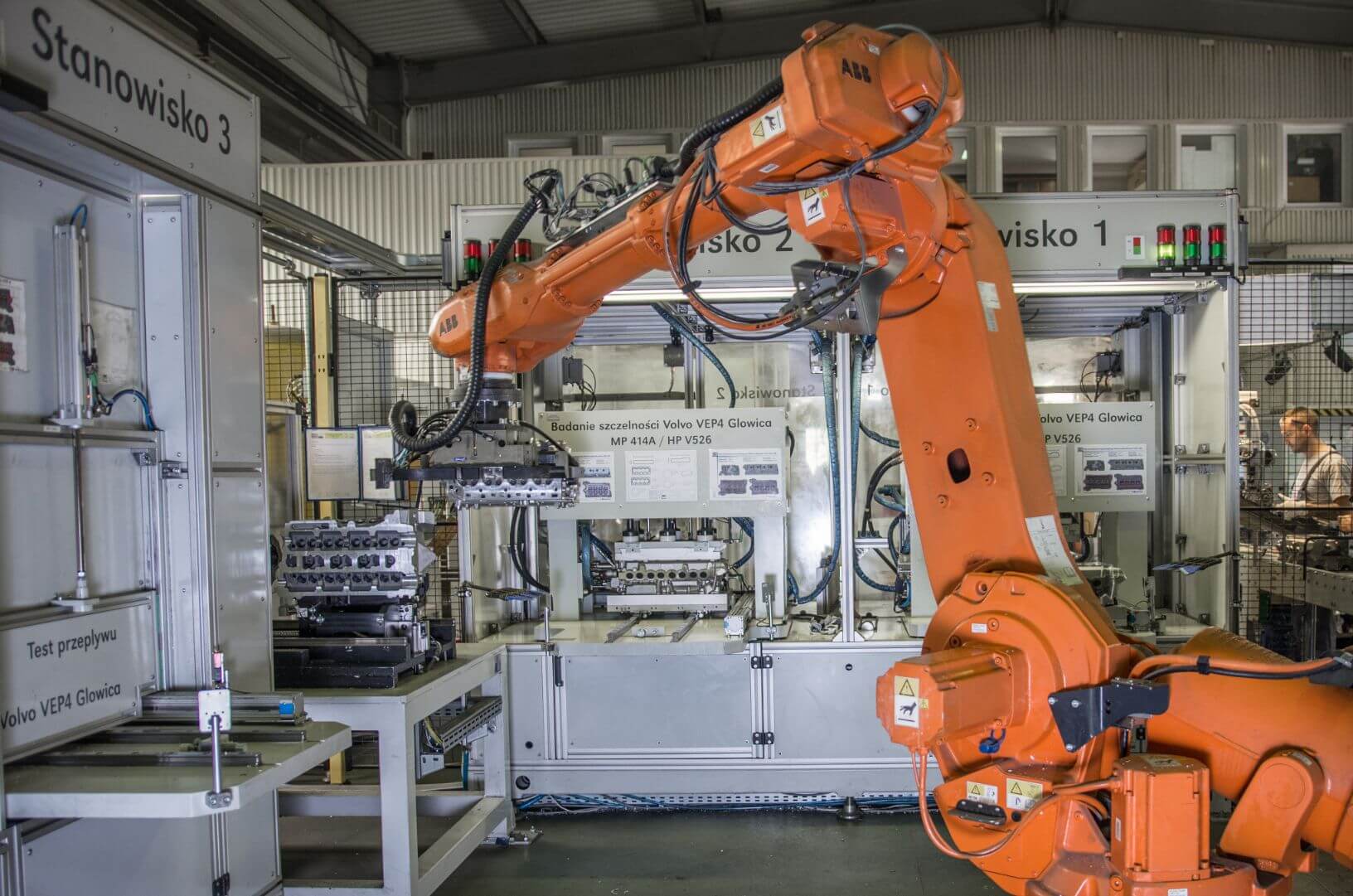