Jak produkować mądrze oto jest pytanie. Ciągła optymalizacja to hasło przewodnie japońskiej filozofii Lean Management oraz zachodniego WCM czyli World Class Manufacturing. Celem jest produkcja szybsza, lepsza oraz tańsza. Podstawą jest osiągnięcie lepszej jakości przedmiotów obrabianych, eliminacji wszelkich strat czy ogólnej redukcji czasu skrawania i czasu przygotowawczego. Jak osiągnąć zen w obróbce skrawaniem?
Możliwości jest wiele, zazwyczaj najprostsze rozwiązania stają się najlepsze. Dziś opowiem o kilku sprawdzonych rozwiązaniach, które znajdą zastosowanie w każdej produkcji.
Ale zacznijmy od podstaw – czym jest Lean Manufacturing? Jest to szczupła produkcja oparta na mądrej i sprytnej pracy. Podstawą jest ciągłe doskonalenie i realizowanie w praktyce zasady Deminga – Plan, Do, Check, Act czyli realizacja działań w czterech ciągle powtarzających się krokach. Rozpocznij od zaplanowania czynności, następnie wprowadź działanie na małą skalę i oceń czy otrzymałeś zamierzone rezultaty. Jeżeli efekt jest zadowalający czas na wprowadzenie działania na szeroką skalę, jeżeli nie – zacznij proces od początku skupiając się na optymalizacji.
Czego należy się wystrzegać? 7 wielkich marnotrawstw czyli z japońskiego muda:
- Nadprodukcji
- Zapasów
- Zbędnego transportu
- Zbędnego ruchu
- Wszelkich braków
- Oczekiwania
- Nadjakości
Warto wspomnieć o ósmej mudzie czyli o utraconym potencjale. Na produkcji często spotyka się wartościowych pracowników, których umiejętności i ich możliwości nie są w pełni wykorzystane i rozwijane.
Wiemy czego unikać ale czy wiemy co jest najważniejsze w każdej produkcji? Mowa o wartości dodanej czyli działaniach, które w sposób bezpośredni wpływają na cechy użytkowe produktu za które chce zapłacić klient.
Po krótkim wstępie teoretycznym czas na przykłady optymalizacji.
1. 5S oraz Standaryzacja
Często mówi się, że najłatwiej zacząć od… sprzątania! Dlaczego? Ponieważ wprowadzenie 5S na produkcji zazwyczaj nie wymaga nakładu finansowego a efekty widać od razu. Co zatem kryje się pod enigmatycznym skrótem 5S? Seiri – Seiton – Seiso – Seiketsu – Shitsuke czyli Selekcja, Systematyka, Sprzątanie, Standaryzacja, Samodyscyplina. Po pierwsze selekcja – w tym kroku warto podzielić wszystkie przedmioty na stanowisku pracy na takie, z których korzystamy często i rzadko oraz przydzielić im odpowiednie miejsce. Następnie systematyka – miejsce na wszystko i wszystko na swoim miejscu czyli czas na dobrą wizualizację. Przydadzą się kolory, taśmy, zdjęcia, tablice wszystko co ułatwi organizację. Trzeci krok – sprzątanie wg. trzech wytycznych – kiedy? / kto? / czym?. Pomocne tutaj będą harmonogramy. Następnie standaryzacja jako jeden z najważniejszych etapów. To w tym momencie wszystkie poprzednie kroki zostają zebrane w jedną przejrzystą całość. Ostatni krok czyli samodyscyplina zamyka 5S. Audyt (przegląd) jest niezbędny, ponieważ dzięki nim możemy utrzymywać jakość wypracowanych standardów.
Skorzystaj z naszych usług obróbki CNC.
2. Diagram Spaghetti odpowiedzią na dobre usytuowanie obrabiarek.
Wyobraźmy sobie prosty proces – półfabrykat na wejściu znajduje się w magazynie. Operator pobiera surowiec i zmierza przez całą halę do pierwszej obrabiarki. Uświadamia sobie, że nie ma wszystkich potrzebnych narzędzi – idzie do narzędziowni. Po wstępnej obróbce zanosi detal do kontroli pomiarowej. Okazuje się, że maszyna jest zajęta i operator musi czekać. Po pomiarze zanosi detal do kolejnej obrabiarki znajdującej się na innej hali produkcyjnej. Po finalnej obróbce detal znów wraca do kontroli pomiarowej po czym zmierzona część trafia do magazynu gotowa do wysłania klientowi. Po tym opisie już wiadomo, że cały proces można zoptymalizować.
Analizując wszystkie przejścia operatora, można rozrysować diagram spaghetti. Pozwala on na analizę przebytej drogi w tym przypadku operatora i znalezieniu mudy.
Możliwości optymalizacji opisanego przykładu jest wiele – poniżej przedstawię kilka:
- Po pierwsze ograniczenie ruchu operatora. Przygotowanie stanowiska przed obróbką znacząco skraca czas. W tym przypadku półfabrykat powinien zostać przetransportowany na stanowisko przez magazyniera a wszystkie narzędzia potrzebne do realizacji zadań powinny wcześniej znajdować się przy stanowisku pracy.
- Po drugie – wyeliminowanie nadjakości oraz czekania. Przedstawiony operator zanosi część po pierwszej obróbce do kontroli pomiarowej. Warto zastanowić się czy ten krok jest konieczny – może wystarczy samokontrola na stanowisku pracy?
- Po trzecie – odległość pomiędzy kolejnymi obrabiarkami. Relokacja ogromnych maszyn nie należy do najłatwiejszych zadań ale przemyślana i zaplanowana zmiana miejsca może przynieść ogromne oszczędności czasu a co za tym idzie – wzrost produktywności i pieniędzy.
W następnej części – szczegółowe spojrzenie na czas skrawania w filozofii Lean, szybkie przezbrojenia oraz TPM odpowiedzią na efektywny park maszynowy.
Natalia Matuszczyk
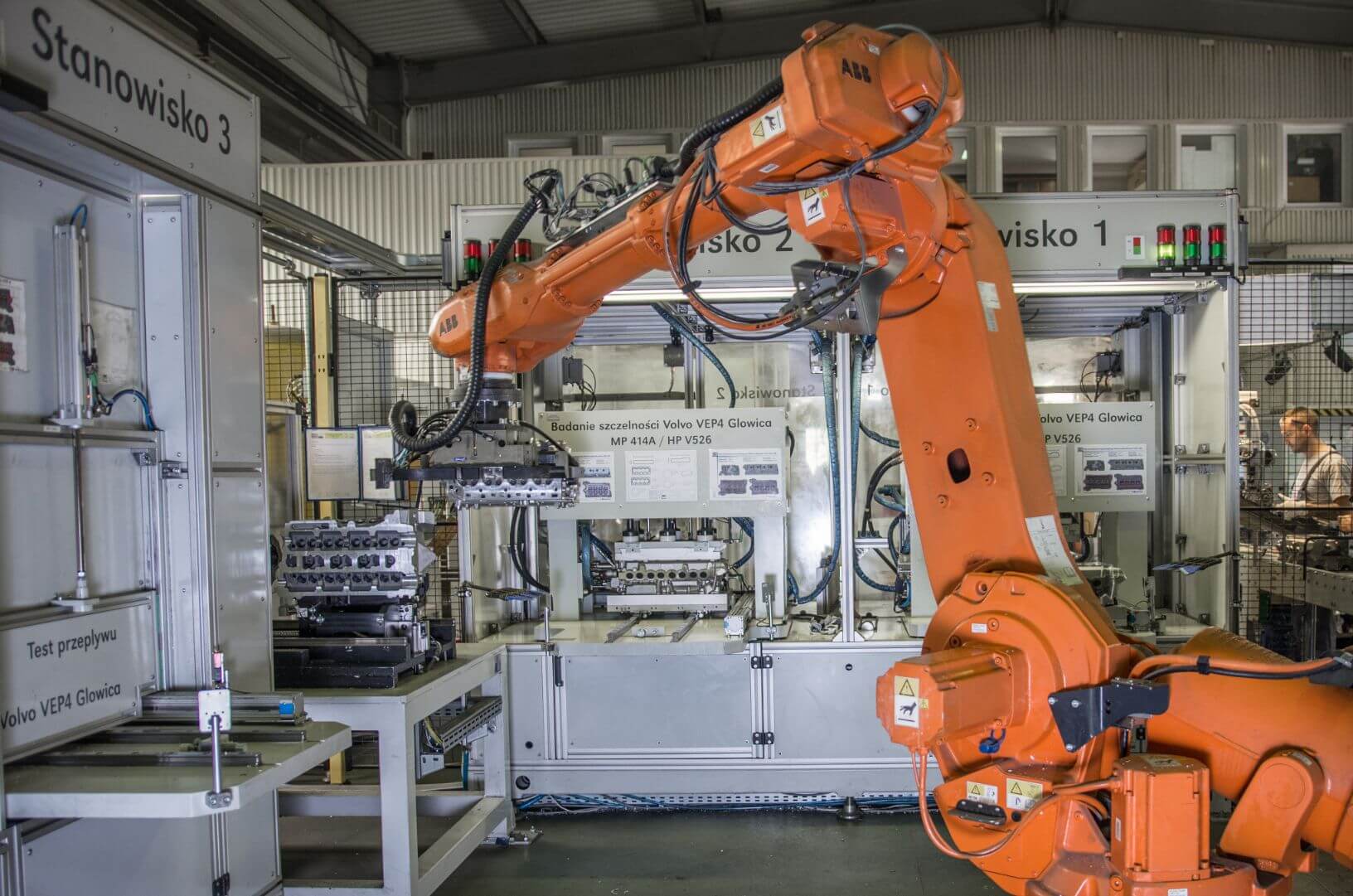