Machining, i.e., processing aimed at changing the shape of an object by removing individual layers of machining allowance, can take various forms. One of the simpler ones is drilling. The tool, in this case a drill, is positioned on a specific point and then a hole is made. Another method would be milling, in which the cutter is set in rotation. The third form of subtractive machining that is undoubtedly worth highlighting is turning. In any production plant that provides professional machining services, there should be a turning service with the use of modern CNC technology.
Metal parts turning – see how!
In milling, the tool rotates, but with turning is differently. It is our object, which we want to give the desired shape, rotates around its axis, while the turning knife, drill or threading tools perform the feed motion. As in the case of other methods of metalworking, precision is also extremely important here. A lathe, which is manually operated by an operator, most likely will not be able to cope with this responsible task when it comes to the execution of a larger order. Therefore, nowadays, most modern enterprises decide to introduce CNC technology into their machine park.
Computerized Numerical Control, or the abbreviation CNC, refers to computer-controlled numerical devices. As you might guess, a modern lathe can also be such a machine. Thus, CNC turning will not require too much commitment when it comes to manual work, because it will be made by the tools themselves. However, you should be familiar with the programming language in order to issue the appropriate commands using a special application.
CNC turning services
In which industries entrepreneurs most often turn to production plants to use CNC turning services? Rather, the relevant question should be in which business sectors turning does not apply. CNC machining is a key factor driving the construction, automotive, furniture and agriculture industries. Thanks to turning, many different components can be created, although it is worth noting that most of them are round or cylindrical in shape. The end products of this process can be, for example, shafts, axles, bushings, bearings, and gears. In contrast, there is also a machining method called boring, which involves turning internal surfaces.
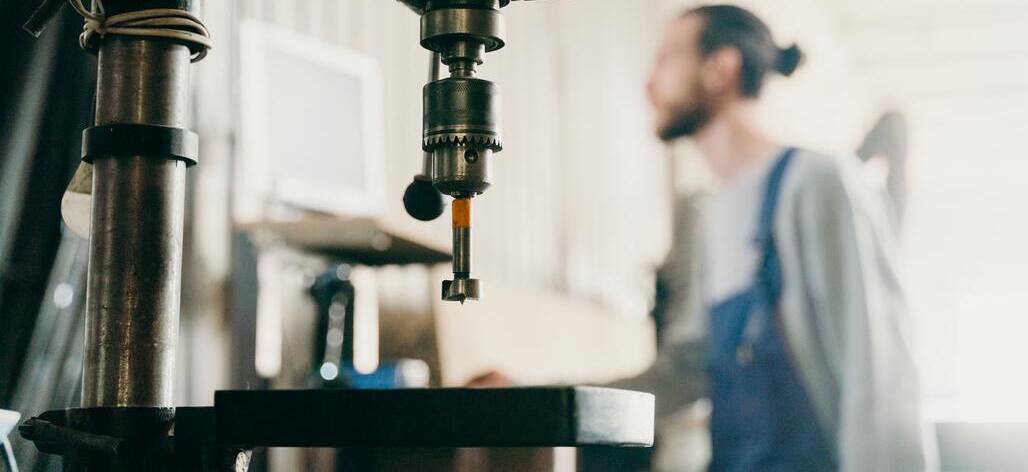