Those entrepreneurs who know what solutions will allow them to achieve their goals cheaper and faster will survive in business. Therefore, structures such as steel halls enjoy unflagging interest on the part of companies from the automotive, construction and agriculture industries. They can be used as a storage area, work space, cover for equipment and vehicles, but in reality there are many more applications for such objects. The erection of such a hall is usually also less time-consuming and costly than erecting a wooden or brick structure. What else is worth knowing about such objects and the process of their formation?
Steel halls – the choice of raw material matters
The raw material from which the hall is made has an impact on the durability and possible applications of the entire facility. Therefore, steel is a very common choice these days. This material is an alloy of iron with carbon and the addition of other elements. May contain chromium, nickel, manganese, copper and titanium. The composition will have an impact on the properties, so a special type of alloy, i.e. structural steel, is most often selected to create steel structures. It is easy to process and resilient, and at the same time hard and durable. One of the reasons why steel halls are chosen today instead of alternative solutions is also the possibility of carrying out works regardless of weather conditions. Therefore, there is no need to plan construction for a specific season.
Welding of steel structures – how are halls created?
The construction of a steel hall should be supervised primarily by specialists who know their stuff. Of course, the client can have a significant impact on the entire process because he provides documentation with the necessary guidelines to the construction and design office. Thanks to the indications, an executive design is created, and then an order for the necessary raw materials is placed. The next stages are primarily the management of the delivered material, unloading, transfer to the raw material warehouse, and then to the workstations. The next step is welding, which is performed by designated employee. A great advantage is the possession of the European Welding Engineer Certificate. Painting, sandblasting or galvanizing are available forms of finishing a steel hall, which are to additionally protect it. The last thing that needs to be taken care of is the as-built documentation, i.e. a certificate confirming compliance with EU standards. Such a certificate proves the professionalism of the company responsible for the implementation of the project.
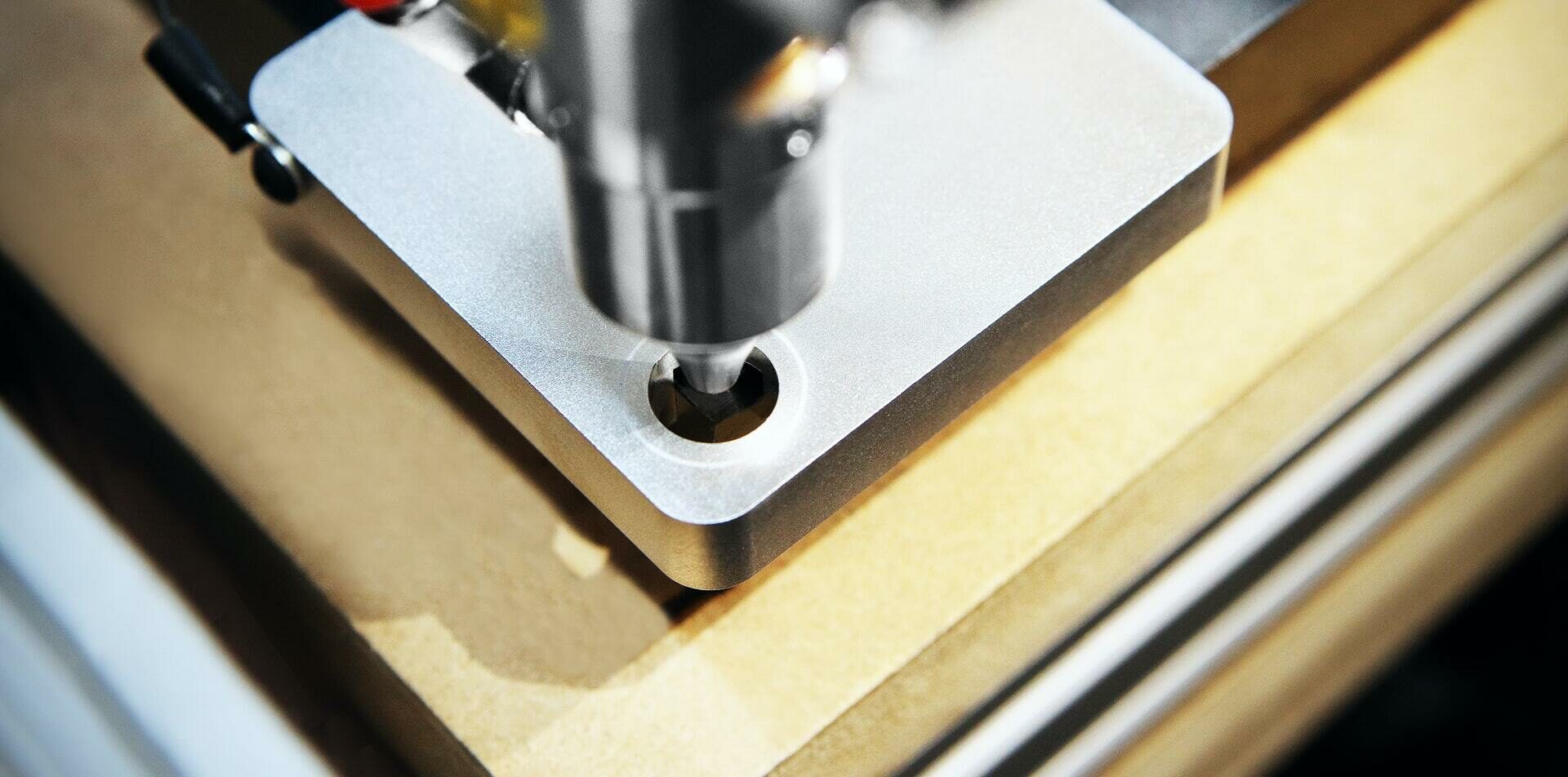