Wie soll man klug produzieren? Das ist die Frage. Ständige Verbesserung ist das Leitmotiv der japanischen Philosophie Lean Management und des westlichen WCM-s das heißt World Class Manufacturing. Das Ziel ist die Produktion zu beschleunigen, zu verbessern und günstiger zu machen. Die Grundlage ist bessere Qualität der bearbeiteten Teilen zu erzielen, die Verluste zu eliminieren und Vorbereitungs- und CNC-Bearbeitungszeit zu reduzieren. Wie ist „zen“ in der CNC-Bearbeitung zu erzielen?
Es gibt viele Möglichkeiten dazu, meistens sind die einfachsten Lösungen die besten. Heute beschreibe ich einige geprüfte Lösungen, die in jeder Produktion Anwendung finden.
Aber beginnen wir von den Grundlagen – was ist Lean Manufacturing? Es ist eine schlanke Produktion, die auf kluger und schlauer Arbeit beruht. Die Basis ist die kontinuierliche Verbesserung und den Grundsatz Deminga – Plan, Do, Check, Act in der Praxis zu realisieren, das heißt die Realisation von vier Maßnahmen in vier Schritten, die ständig wiederholt werden. Fange mit dem Planen der Tätigkeit an, danach führe die kleine Handlung ein und beurteile, ob du die anstrebenden Ergebnisse erreicht hast. Falls das Ergebnis dich zufrieden stellt, dann ist das der richtige Zeitpunkt die übergreifende Tätigkeiten einzuführen, falls dieser Zeitpunkt noch nicht gekommen ist, beginne mit dem Prozess vom Anfang an indem du dich an der Verbesserung konzentrierst.
Was soll man vermeiden? Die 7 großen Verschwendungsarten – aus dem Japanischen Muda:
- Überproduktion
- Bestände
- überflüssiger Transport
- unnötige Bewegungen
- jegliche Mängel
- Erwartungen
- Überqualität
Erwähnenswert ist das achte Muda also das verlorene Potential. In der Produktion trifft man oft wertvolle Mitarbeiter, derer Qualifikationen und Möglichkeiten nicht vollständig eingesetzt und entwickelt werden.
Wir wissen, was zu vermeiden ist aber ist es uns klar, was in jeder Produktion am wichtigsten ist? Es ist die Rede von den hinzugefügten Vorteil – die Aktionen , die direkt die Eigenschaften des Produktes beeinflussen, für die der Kunde bezahlen will.
Nach der kurzer Einführung ist die Zeit gekommen die Verbesserungsbeispiele zu zeigen.
- 5S und Standardisierung
Oft sagt man, dass es am einfachsten ist vom….Aufräumen anzufangen! Warum? Weil die Einführung von 5S in der Produktion meistens keiner finanziellen Mittel bedarf und die Ergebnisse sind gleich zu sehen. Was versteckt sich hinter dem enigmatischen Begriff 5S? Seiri – Seiton – Seiso – Seiketsu – Shitsuke bedeuten Selektieren, Systematisieren, Säuberung, Standardisieren und Selbstdisziplin. Erstens Selektieren – in diesem Schritt lohnt es sich alle Arbeitsgegenstände auf dem Arbeitsplatz in solche zu teilen, die wir oft und selten benutzen und denen einen entsprechenden Platz einzuräumen. Dann Systematisieren – ein Platz für alles und alles auf seinem Platz also Zeit für gute Visualisierung. Nützlich sind in diesem Schritt Farben, Bänder, Fotos, Tafel, das was die Organisation vereinfacht. Der dritte Schritt – Säuberung gem. den 3 Anweisungen – wann? / wer? / womit? Hilfreich sind hier die Arbeitspläne. Dann Standardisieren als eine der wichtigsten Etappen. Eben jetzt bilden frühere Schritte eine klare Einheit. Der letzte Schritt – Selbstdisziplin schließt 5S ab. Das Audit (Übersicht) ist notwendig, weil dadurch die Qualität der erzielten Standards einzuhalten ist.
- Spaghetti- Diagramm eine Antwort auf gute Lokalisierung der Werkzeugmaschinen.
Stellen wir uns ein einfacher Prozess – ein Fertigteil am Wareneingang befindet sich auf Lager. Der Maschinist nimmt das Rohmaterial und bewegt sich durch die ganze Halle bis zur ersten Werkzeugmaschine. Es wird ihm klar, dass er nicht alle notwendigen Werkzeuge dabei hat – er geht zum Werkzeuglager. Nach vorläufiger Bearbeitung bringt er das Teil zur Vermessungskontrolle. Es zeigt sich, dass die Maschine besetzt ist und der Maschinist warten muss. Nach der Vermessung bringt er das Teil zur nächsten Werkzeugmaschine, die sich in einer anderen Halle befindet. Nach der finalen Bearbeitung kehrt er zur Vermessungskontrolle zurück, danach kommt das Teil nach der Vermessung zum Lager zwecks Lieferung an den Kunden. Diese Beschreibung macht uns bewusst, dass der ganze Prozess verbessert werden kann.
Bei der Analyse aller Schritten des Maschinisten kann man das Spaghetti-Diagramm zeichnen. Es lässt die zurückgelegte Strecke des Maschinisten zu analysieren und Muda zu finden.
Es gibt viele Möglichkeiten das beschriebene Beispiel zu analysieren – nachstehend einige:
- Erstens sollen die Bewegungen des Maschinisten reduziert werden. Die Vorbereitung des Arbeitsplatzes vor der Bearbeitung verkürzt wesentlich die Zeit. In diesem Fall sollte das Fertigteil zur Station vom Lageristen transportiert werden und alle notwendigen Werkzeuge für die Abwicklung der Aufgaben sollten früher auf dem Arbeitsplatz vorbereitet werden.
- Zweitens – die Überqualität und die Wartezeit sollen behoben werden. Der Maschinist bringt das Teil zur Vermessungskontrolle. Es ist überlegenswert, ob dieser Schritt notwendig ist – es kann sein, dass die Selbstkontrolle auf dem Arbeitsplatz ausreichend ist?
- Drittens – die Entfernung zwischen nächsten Werkzeugmaschinen. Die Standortänderung der großen Maschinen ist keine einfache Aufgabe aber gut überlegte und geplante Änderung kann große Zeitersparnisse mit sich bringen und folglich – Produktivität- und Gewinnsteigerung.
Natalia Matuszczyk
Im nächsten Teil – wird die Zeit der CNC-Bearbeitung in der Lean Philosophie unter die Lupe genommen, schnelle Umrüstungen und TPM las eine Antwort auf einen effektiven Maschinenpark.
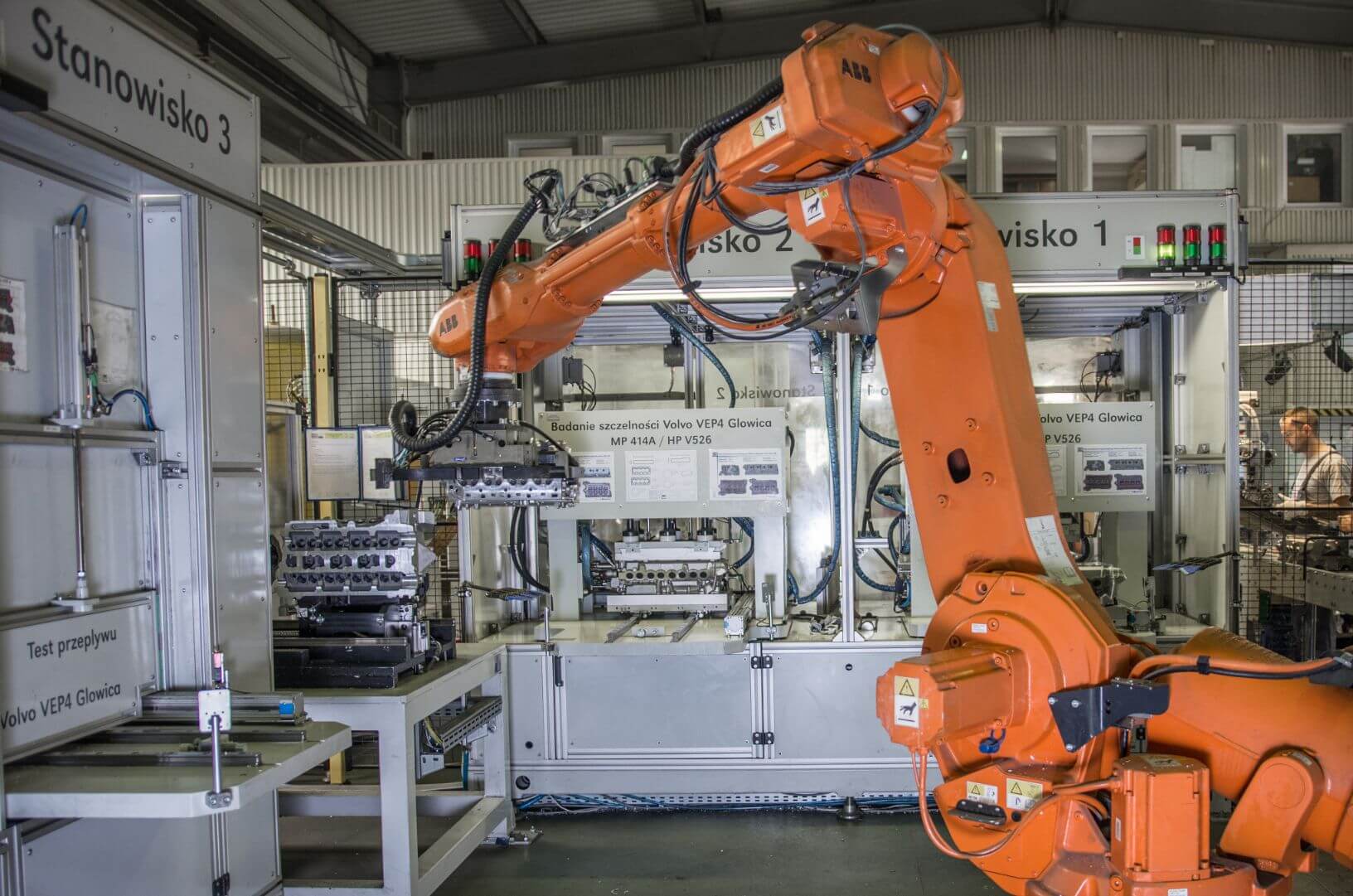