Lean Management w obróbce skrawaniem coraz częściej ma zastosowanie nie tylko w ogromnych korporacjach, ale również w małych rodzinnych firmach. Dzieje się tak, ponieważ dobre rozwiązania i standardy pracy przynoszą spore oszczędności małym kosztem. Liczy się efekt, dlatego warto zastanowić się czy chcemy rozmawiać o SMEDzie, KAIZEnie, 5S, TPMie czy po prostu i po ludzku o szybkich przezbrojeniach, o dobrych bezkosztowych pomysłach na usprawnienia, organizacji stanowisk pracy i wszystkich ważnych czynnościach związanych z konserwacją i obsługą maszyn. Prościej, prawda?
Po przeczytaniu ostatniego artykułu wiemy, że najważniejsze to skupić się na wartości dodanej oraz wyeliminować możliwie wszystkie marnotrawstwa. Ile różnych produkcji, technologii tak inne będzie podejście i metody wprowadzania LEANu. Jak to dokładnie wygląda w świecie obróbki skrawaniem?
Po pierwsze – co jest naszą podstawową wartością dodaną. Patrząc na prostą definicję, czyli ‘za co chce zapłacić klient’ to odpowiedzią jest detal obrobiony. Czyli najważniejszym czasem jest czas skrawania. Zastanawialiście się kiedykolwiek ile procent całego dostępnego czasu w ciągu roku zajmuje sam czas obróbki skrawaniem*? 60%? Byłoby świetnie. Może 35%? Blisko. Odpowiedź daje wiele do myślenia. Statystycznie TYLKO 24% to czas wartości dodanej. Jak to możliwe? Rozpatrując, że w ciągu roku mamy dostępnych 8760 godzin 60% to czas związany z produkcją. W tym czasie oprócz czasu maszynowego, który wynosi 50% ukryte są też przezbrojenia, awarie, wymiany detalu oraz postoje, które są czasem straconym. Idąc dalej w czasie maszynowym nie mamy samej obróbki skrawaniem – wymiana narzędzi, pozycjonowanie to również czas stracony. Reasumując, iloczyn czasu związanego z produkcją, czasu maszynowego i czasu skrawania wynosi 24%.
Rys. 1. Rozkład czasu wartości dodanej w obróbce skrawaniem (opracowanie własne, dane statystyczne z firmy Sandvik Coromant)
Po drugie – wybranie metody, która znacząco skróci czas niebędący wartością dodaną. Polecam SMED – Single Minute Exchange of Die. Obrabiarka jedna, procesów wiele – dążymy do redukcji czasu związanego z przezbrojeniem do jednocyfrowej liczby minut. Przezbrojenie to czas, który upływa pomiędzy ostatnim, dobrym detalem poprzedniej produkcji a pierwszym, dobrym detalem nowej produkcji. Historycznie patrząc, pierwsza odnotowana próba wykorzystanie metodologii SMED udała się w Japonii w przemyśle stoczniowym Toyoty gdzie zredukowano czas przezbrojenia 1000 tonowej prasy z 4 godzin do 3 minut! Dobrze ale, od czego zacząć? W pierwszej fazie należy podzielić wszystkie czynności na wewnętrzne i zewnętrzne. Czynności, które można wykonać tylko przy wyłączonej maszynie nazywamy wewnętrznymi a pozostałe to czynności zewnętrzne. Gdy podział jest zrobiony, w drugiej fazie próbujemy przekształcić czynności wewnętrzne na zewnętrzne oraz spróbować wyeliminować wszystkie niepotrzebne czynności. Ostatnia faza to poprawa wszystkich czynności, które biorą udział w przezbrojeniu oraz opracowanie planu na dane przezbrojenie. Przykładowo przed zatrzymaniem maszyny dobrze jest przygotować i pomierzyć wszystkie narzędzia, potrzebne do obróbki detalu nowej produkcji. Polecam również zainteresować się nowoczesnymi technologiami mocowań np. „zero-point clamping system” pozwalający na bardzo szybkie przezbrojenia z powtarzalnością pozycjonowania rzędu 2,5 mikrometra**.
Ostatnim ważnym czynnikiem wpływającym bezpośrednio na czas wartości dodanej to stan obrabiarki. Możemy mieć krótkie przezbrojenia, zorganizowane stanowisko pracy, przemyślany proces, ale gdy pojawi się awaria maszyny to tracimy wszystko. Kilka słów o TPM-ie – z angielskiego Total Productive Maintenance czyli Całkowite Produktywne Utrzymanie Ruchu. Głównym celem jest dbałość o techniczny stan maszyn. Kiedy wiadomo, że TPM jest dobrze wdrożony w firmie? Po pierwsze przestajemy „gasić pożary” a zaczynamy zapobiegać ich powstawaniu, po drugie mówimy o świadomości zbiorowej – nie istnieje pojęcie „ja produkuję a ty naprawiasz” – za TPM jest odpowiedzialna cała załoga. Jest osiem filarów, o których polecam poczytać w wolnym czasie natomiast ja chcę się skupić na stratach w TPM, czyli:
- Awarie
- Przezbrojenia
- Mikro przestoje
- Zredukowana prędkość
- Złom
- Rozruch
Punkt 1 i 2 odnoszą się do strat dostępności – wszystkie planowanie i nieplanowane postoje, wymiany narzędzi a także przerwy śniadaniowe zaliczają się do tej grupy.
Punkt 3 i 4 to straty wykorzystania. Ciekawy jest punkt dotyczący zredukowanej prędkości. Prawdą jest, że lepiej, gdy maszyna pracuje na maksymalnej prędkości aniżeli sztuczne się ją spowalnia. Po zajęciach z TPM pamiętam dokładnie jedno krótkie zdanie prowadzącego – „Maszyna ma pracować”.
Ostatnie dwa punkty to straty jakości – wszystkie NOKi, defekty, poprawki to dokładnie ta grupa.
Zobacz: obróbka mechaniczna CNC w naszej ofercie.
Pomocne niewątpliwie będą wskaźniki do określania efektywności parku maszynowego. Najważniejszy to OEE a to nic innego jak iloczyn dostępności, wykorzystania i jakości. Kolejne dwa to MTBF (Mean Time Between Failures), czyli średni czas pomiędzy awariami oraz MTTR (Mean Time to Repair), jako średni czas naprawy.
Metod w LEANie jest dużo, wprowadzanie wszystkich na raz jest po pierwsze niemożliwe, ale również nierozsądne. Tak jak wspominałam, należy zastanowić się, co będzie pomocne w optymalizacji konkretnej produkcji i zrobić ten pierwszy krok. Życzę dobrych i mądrych usprawnień.
Natalia Matuszczyk
*uwaga – dane dla procesów jednostkowych i małoseryjnych. W procesach masowych w pełni zautomatyzowanych procent czasu produkcji/skrawania może wynosić 60%.
** https://www.zeroclamp.com/en/zero-point-clamping-system/
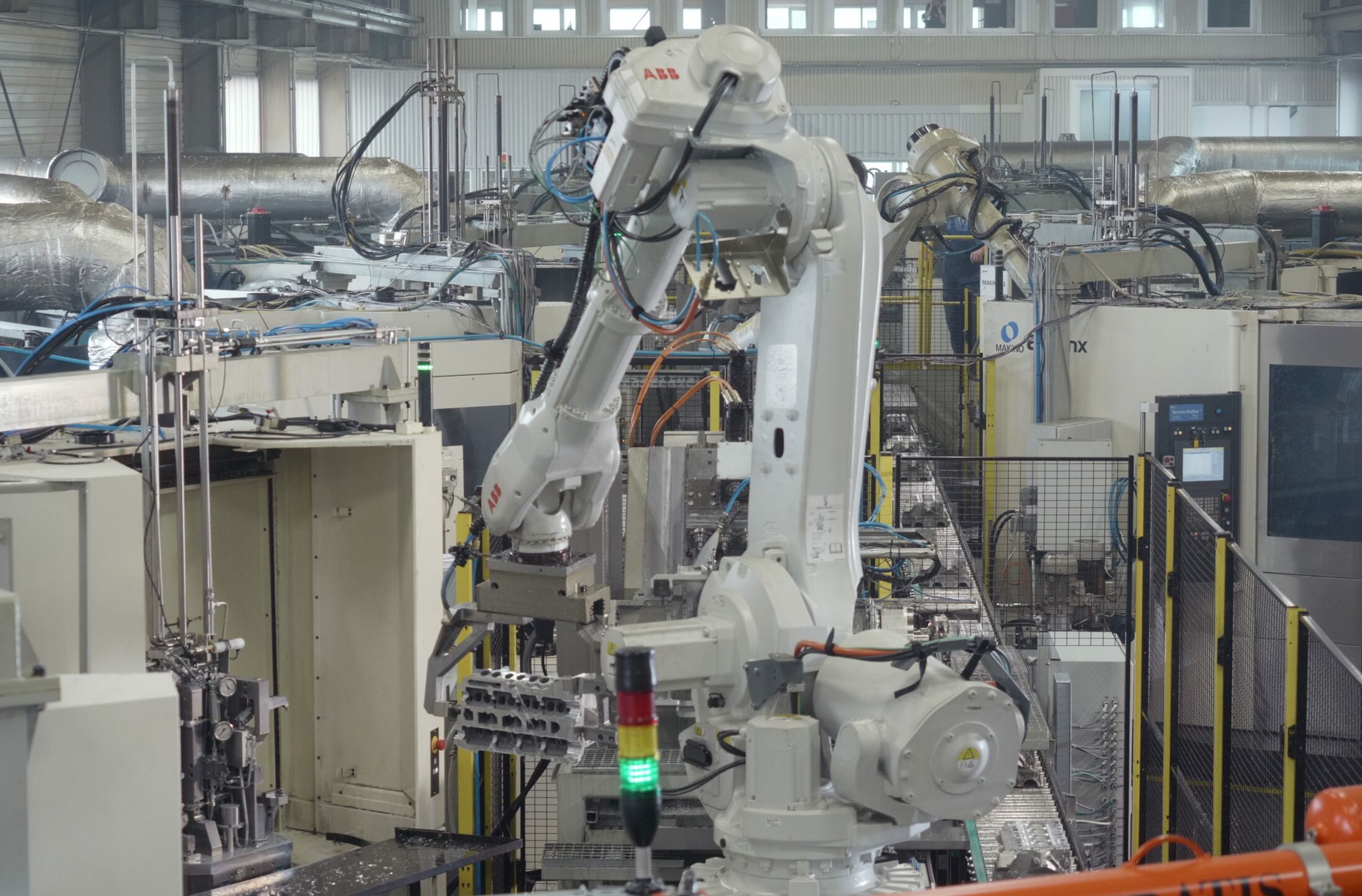