Zapraszam na cykl artykułów dotyczących podstawowych zagadnień z dziedziny obróbki skrawaniem. Jesteśmy świadkami szybkiego rozwoju technologii, jednak, aby móc w pełni zrozumieć zachodzące zmiany, warto posiadać podstawową (czasami historyczną) wiedzę w tej dziedzinie. Jeżeli jesteś pasjonatem skrawania to mam nadzieję, iż kolejne teksty będą miłym przypomnieniem. Natomiast, jeżeli dopiero stawiasz pierwsze kroki w obszarze CNC to wierzę, że dowiesz się kilku ciekawych rzeczy. Zaczynajmy!
Który proces jest prostszy – toczenie czy frezowanie? Pytanie podchwytliwe, otóż odpowiedziałabym przewrotnie, że wiercenie. Dlaczego? Od strony programowania jest to tylko jeden blok, no może dwa. Wjazd na G1, wyjazd na G0. Dziękuję, to wszystko na dziś.
Żartowałam. W istocie mogłoby się wydawać, że jest to mało skomplikowana operacja. Otóż nie. Mnogość problemów, jakie możemy napotkać może zniechęcić – złamane wiertła, zła jakość otworu, bicie narzędzia, zły wymiar, krótka żywotność, a co za tym idzie – wysoki koszt na sztukę, zaplątane długie wióry na wiertle i wiele innych problemów. Spróbuję dać kilka wskazówek jak podejść do tematu wiercenia, aby w sposób świadomy wyeliminować wyżej wymienione problemy.
Zacznijmy jednak od krótkiej teorii. W przypadku wiercenia, ale też rozwiercania, gwintowania, pogłębiania mówimy o sterowaniu punktowym (point – to – point control). Zasada jest prosta, narzędzie jest pozycjonowane na zadany punkt ruchem szybkim, następnie obróbka wykonywana jest ruchem roboczym w jednej osi (zazwyczaj w osi Z) (rys. 1a).
Rys. 1. a) Sterowanie punktowe, b) Rozkład sił skrawania przy wierceniu [źródło „Programowanie Obrabiarek CNC” W.Grzesik, P.Niesłony, P.Kiszka; „Obróbka Skrawaniem” K. Jemielniak]
Kinematycznie rzecz biorąc wyróżnia się w wierceniu siłę osiową oraz moment obrotowy (rys. 1b). Siła osiowa to suma sił posuwowych Ff1 i Ff2, moment natomiast uzyskany jest z sił Fc1 i Fc2. Na rysunku widać jeszcze siły odporowe, natomiast w tym przypadku redukują się one wzajemnie. (Uwaga dla pasjonatów – jeżeli jeszcze jakimś cudem nie znacie świetnej pozycji „Obróbka Skrawaniem” Krzysztofa Jemielniaka to polecam nadrobić zaległości – siły skrawania, kąty w układzie narzędzia, materiały narzędziowe i wiele innych – dla koneserów czystej teorii).
Pierwszy problem wiercenia jest taki, że nic nie widać podczas skrawania. Podjeżdżamy wiertłem, pozycjonujemy i jedyne, czego jesteśmy pewni to odległości wiertła od przedmiotu obrabianego. Następnie wjazd w materiał i wyjazd. Jak zatem ocenić czy jest ok? Po pierwsze dźwięk – powinien być jednolity, gładki. Po drugie kontrola wiórów – powinny być stosunkowo krótkie w kształcie litery C. Po trzecie, jakość otworu oraz jego wymiary i zgodność z tolerancją. Po czwarte obserwacja narzędzia – przetarcia, zużycia, narosty mogą szybko wskazać na problem występujący w procesie. Bardzo często wystarczy zmiana parametrów, aby uzyskać zadowalający efekt. Zwiększenie posuwu oraz chłodzenie wewnętrzne często rozwiązuje problem długich wiórów. Zwiększenie vc wyeliminuje narost a zmiana oprawki z ER na hydrauliczną spowoduje, że mocowanie będzie bardziej precyzyjne, a bicie zmniejszone przez co narzędzie zyska na trwałości. Polecam wnikliwą obserwację procesu nawet tak prostego jak wiercenie.
Drugi problem wiercenia pojawia się na samym początku, a mianowicie problem doboru odpowiedniego wiertła do danego zadania produkcyjnego. Aby wybrać odpowiednie wiertło warto odpowiedzieć sobie na kilka podstawowych pytań. Na jakiej obrabiarce będziemy wiercić? Jaki jest materiał obrabiany? Jaką tolerancję otworu trzeba uzyskać? Jak długi ma to być otwór – 2D? A może aż 18D? Ile jest otworów do wykonania – czy jest to produkcja masowa czy jednostkowa? Asortyment jest duży, ale co wybrać? Jeżeli jest do wykonania duży otwór o średnicy powyżej 20 mm to podstawowym wyborem będzie wiertło na płytki. Najmniej dokładne, ale do wielu zadań obróbkowych wystarczające. Przypadek przeciwny – duża seria, mała średnica, ważna dokładność w tym przypadku lepiej wybrać wiertło monolityczne pełno węglikowe. Zdecydowanie najdroższy wybór na start natomiast długa żywotność i wysoka jakość otworu zrekompensują wstępną inwestycję. Są jeszcze wiertła z wymienną węglikową końcówką, które są kompromisem pomiędzy wspomnianymi wcześniej wiertłami. Charakteryzują się większą dokładnością od wierteł na płytki, a ze względu na stalowy korpus są odporniejsze na potencjalne błędy w użytkowaniu od wierteł węglikowych. Wybór wiertła nie jest łatwy, najlepiej przed zakupem skontaktować się z dostawcą narzędzi.
Trzeci problem, o którym wspomnę dotyczy wiercenia długich otworów. Jak wywiercić otwór np. o długości 12xD? Na pewno potrzebne jest stabilne mocowanie i odpowiednia precyzyjna oprawka. Pierwsze narzędzie to pilot, czyli małe sztywne wiertło, które wykona otwór na głębokość 1,5xD. Następnym narzędziem jest długie wiertło, które wprowadza się do otworu pilotowego na zredukowanych parametrach oraz z wyłączonym chłodzeniem wewnętrznym. Ma to na celu redukcję drgań narzędzia. Po uzyskaniu długości 1,5xD wiercenie przebiega na docelowych parametrach skrawania z włączonym chłodzeniem. Ważna uwaga! W tym przypadku narzędzie podczas wyjazdu powinno pracować na zmniejszonych obrotach oraz odpowiednim posuwie roboczym, niestety nie na posuwie G0. Ten czas jest bardzo często pomijany podczas szacowania czasu obróbki. Reasumując – konieczna jest dobra strategia.
Na koniec wspomnę tylko, że cykle ułatwiają cały proces programowania. Najczęściej wybierany to G81, czyli standardowe wiercenie. Jeżeli wiercimy długi otwór np. wiertłem z HSS no to cykle takie jak G83 lub G73 są świetnym wyborem. Widzisz problem przy wierceniu z pogłębianiem? Brakuje zatrzymania na dnie? Proszę bardzo – cykl G82 rozwiąże ten problem.
Przedstawiłam kilka mam nadzieję ciekawych aspektów obróbki, jaką jest wiercenie. Na pierwszy rzut oka prostego i niewymagającego zabiegu jednakże obfitującego w szczegóły.
Natalia Matuszczyk
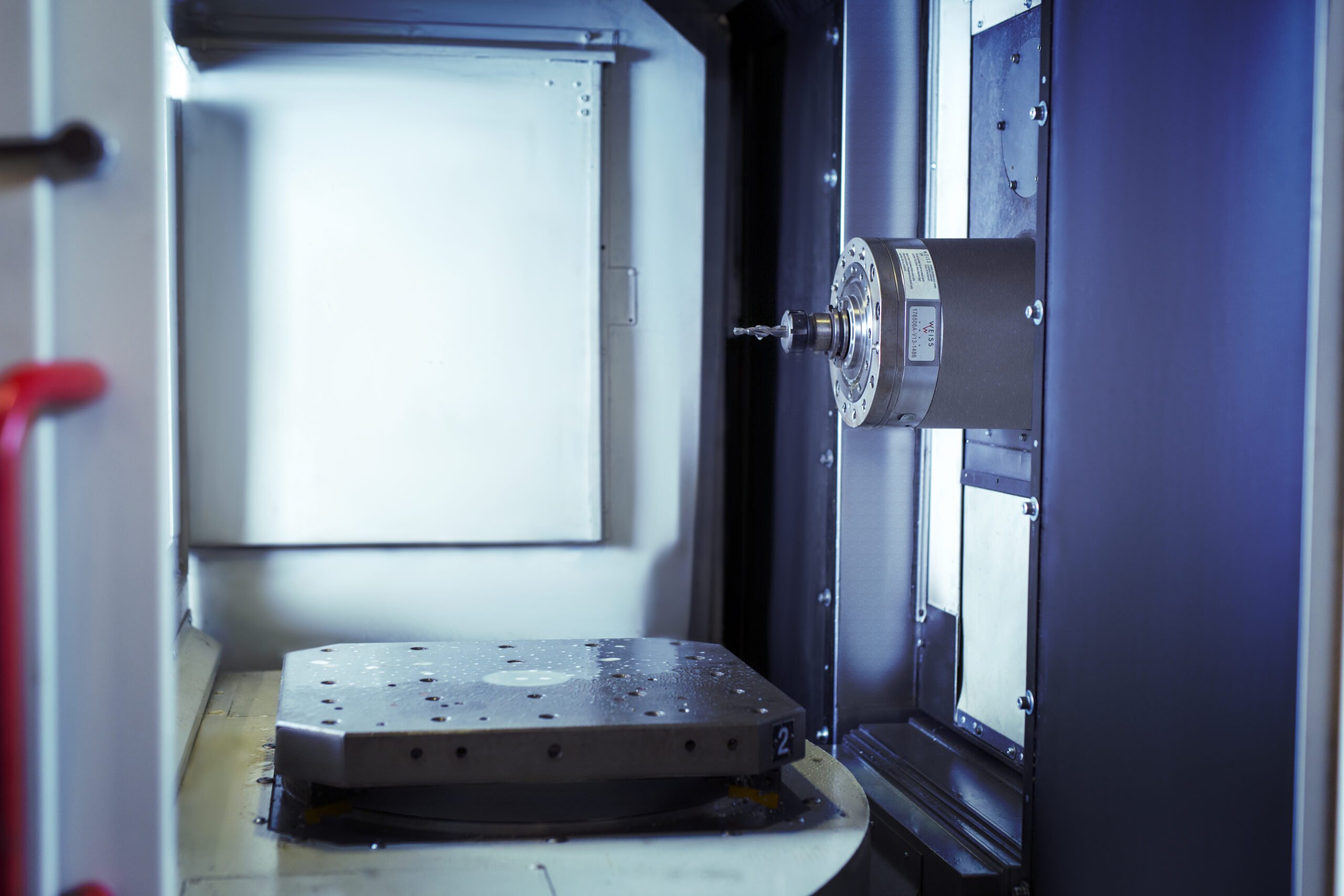