Ich lade Sie zu einer Artikelserie über die Grundlagen der Spanbearbeitung ein. Wir sind Zeugen einer rasanten Entwicklung der Technologie, aber um die stattfindenden Veränderungen vollständig zu verstehen, ist es nützlich, das grundlegende (manchmal historische) Wissen über dieses Gebiet zu haben. Wenn Sie sich für die Spannbehandlung begeistern, hoffe ich, dass die folgenden Texte eine nette Erinnerung sein werden. Wenn Sie jedoch gerade die ersten Schritte im CNC-Bereich machen, glaube ich, dass Sie einige interessante Dinge erfahren werden. Lassen Sie uns beginnen!
Welches Verfahren ist einfacher – Fräsen oder Drehen? Es ist eine Fangfrage, ich würde also unerwartet das Bohren nennen. Warum? Auf der Programmierseite ist es nur ein, na ja, vielleicht zwei Blöcke. Eintritt bei G1, Austritt bei G0. Danke, das war’s für heute.
Das war nur ein Scherz. In der Tat könnte es wie eine unkomplizierte Operation aussehen. Dem ist nicht so. Die Vielzahl der Probleme, auf die wir stoßen können, kann entmutigend sein – gebrochene Bohrer, schlechte Bohrungsqualität, Werkzeugauslauf, falsche Dimension, kurze Lebensdauer und damit hohe Stückkosten, verhedderte lange Späne am Bohrer und viele andere Probleme. Ich werde versuchen, einige Tipps zu geben, wie man das Thema Bohren angehen kann, um die oben genannten Probleme bewusst zu beseitigen.
Beginnen wir jedoch mit einer kurzen Theorie. Beim Bohren, aber auch beim Aufbohren, Gewindeschneiden, Senken spricht man von Punktsteuerung (point – to – point control). Das Prinzip ist einfach, das Werkzeug wird mit einer Eilgangbewegung an einem bestimmten Punkt positioniert, dann erfolgt die Bearbeitung mit einer Arbeitsbewegung in einer Achse (meist in der Z-Achse) (Abb. 1a).
Abb. 1.a) Punktsteuerung, b) Verteilung der Schnittkräfte beim Bohren [Quelle „Programmierung von CNC-Werkzeugmaschinen“]. W. Grzesik, P. Niesłony, P. Kiszka; „Spanbearbeitung” K. Jemielniak]
Kinematisch gesehen wird beim Bohren zwischen Axialkraft und Drehmoment unterschieden (Abb. 1b). Axialkraft ist die Summe der Vorschubkräfte Ff1 und Ff2, während sich das Moment aus den Kräften Fc1 und Fc2 ergibt. In der Abbildung sind die Widerstandskräfte noch zu sehen, aber in diesem Fall reduzieren sie sich gegenseitig. (Ein Hinweis für Enthusiasten – falls Sie durch ein Wunder die hervorragende Position „Spanbearbeitung“ von Krzysztof Jemielniak noch nicht kennen, empfehle ich, das nachzuholen – Schnittkräfte, Winkel in der Werkzeugauslegung, Werkzeugmaterialien und vieles mehr – für Kenner der reinen Theorie).
Das erste Problem beim Bohren ist, dass man beim Spanen nichts sehen kann. Wir fahren mit dem Bohrer, positionieren ihn und das Einzige, worüber wir uns sicher sind, ist der Abstand des Bohrers zum Werkstück. Dann Eintritt ins Material und Austritt. Woran erkennen wir also, ob dies in Ordnung ist? Erstens das Geräusch – es sollte gleichmäßig, glatt sein. Zweitens Überprüfung der Späne – sie sollten relativ kurz und C-förmig sein. Drittens die Qualität der Bohrung sowie ihre Abmessungen und die Einhaltung der Toleranz. Viertens Beobachtung des Werkzeugs – Abrieb, Verschleiß und Verkrustungen können schnell auf ein Problem im Verfahren hinweisen. Sehr oft reicht es aus, die Parameter zu ändern, um einen zufriedenstellenden Effekt zu erzielen. Die Erhöhung der Vorschubgeschwindigkeit und die Innenkühlung lösen oft das Problem der langen Späne. Die Erhöhung von vc eliminiert Verkrustungen und der Wechsel des Spannfutters von ER auf ein hydraulisches Spannfutter führt zu präziserem Spannen und reduziertem Auslauf, was das Werkzeug langlebiger macht. Ich empfehle eine gründliche Beobachtung eines selbst so einfachen Verfahrens wie das Bohren.
Das zweite Problem mit dem Bohren entsteht gleich zu Beginn, nämlich das Problem der Auswahl des richtigen Bohrers für die jeweilige Fertigungsaufgabe. Um den richtigen Bohrer zu wählen, lohnt es sich, ein paar grundlegende Fragen zu beantworten. Auf welcher Werkzeugmaschine werden wir bohren? Was ist das Werkstückmaterial? Welche Bohrungstoleranz müssen wir erreichen? Wie lang soll die Bohrung sein – 2D? Vielleicht sogar 18D? Wie viele Bohrungen sollen hergestellt werden – ist es eine Massenproduktion oder ein Einzelstück? Die Auswahl ist groß, aber was soll man wählen? Wenn eine große Bohrung mit einem Durchmesser von mehr als 20 mm ausgeführt werden soll, ist ein Schneidplattenbohrer die erste Wahl. Am wenigsten genau, aber für viele Bearbeitungsaufgaben ausreichend. Im umgekehrten Fall – große Serie, kleiner Durchmesser, die Genauigkeit ist in diesem Fall wichtig – es ist besser, einen monolithischen Vollhartmetallbohrer zu wählen. Definitiv die teuerste Wahl für den Anfang, wobei die lange Lebensdauer und die hohe Qualität der Bohrung die Anfangsinvestition ausgleichen. Dann gibt es noch Bohrer mit austauschbaren Hartmetallspitzen, die einen Kompromiss zwischen den vorgenannten Bohrern darstellen. Sie sind genauer als Schneidplattenbohrer und aufgrund ihres Stahlkörpers widerstandsfähiger gegen mögliche Bedienungsfehler als Hartmetallbohrer. Die Auswahl eines Bohrers ist nicht einfach, am besten sollte man vor dem Kauf den Werkzeuglieferanten kontaktieren.
Das dritte Problem, das ich erwähnen möchte, betrifft das Bohren von Langlöchern. Wie soll eine Bohrung in einer Länge von 12xD gebohrt werden? Auf jeden Fall sind eine stabile Halterung und ein richtiger Präzisionsrahmen notwendig. Das erste Werkzeug ist ein Pilot, also ein kleiner starrer Bohrer, der eine 1,5xD tiefe Bohrung ausführt. Das nächste Werkzeug ist ein langer Bohrer, der mit reduzierten Parametern und ausgeschalteter Innenkühlung in die Pilotbohrung eingeführt wird. Dies dient der Reduzierung von Werkzeugschwingungen. Sobald eine Länge von 1,5xD erreicht ist, wird das Bohren mit den Ziel-Schnittparametern bei eingeschalteter Kühlung durchgeführt. Wichtige Anmerkung! In diesem Fall sollte das Werkzeug während des Austritts mit reduzierter Drehzahl und dem entsprechenden Arbeitsvorschub laufen, leider nicht mit dem G0-Vorschub. Diese Zeit wird bei der Schätzung der Bearbeitungszeit sehr oft übersehen. Zusammengefasst – eine gute Strategie ist notwendig.
Abschließend möchte ich noch erwähnen, dass Zyklen den gesamten Programmierprozess vereinfachen. Die gebräuchlichste Wahl ist G81, also die Standardbohrung. Wenn wir eine Langbohrung z. B. mit einem HSS-Bohrer bohren, sind Zyklen wie G83 oder G73 eine ausgezeichnete Wahl. Gibt es ein Problem bei der Senkungsbohrung? Fehlt der Boden-Stopp? Bitte sehr – der Zyklus G82 wird dieses Problem lösen.
Ich habe hoffentlich einige interessante Aspekte der Bearbeitung, nämlich das Bohren, dargestellt. Auf den ersten Blick ein einfacher und anspruchsloser Vorgang, der jedoch reich an Details ist.
Natalia Matuszczyk
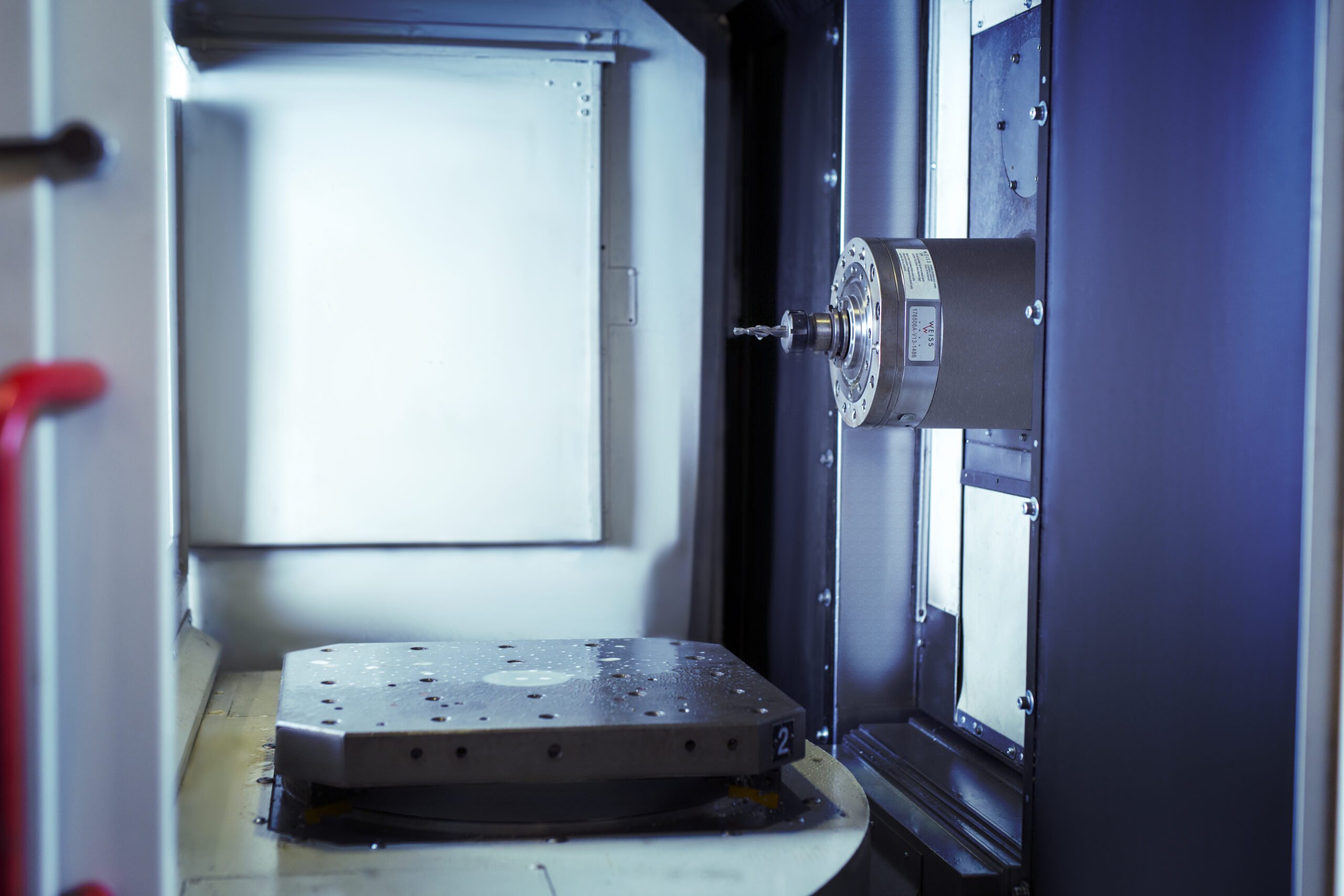