After reading the last article, we know that simple drilling is not that easy. Today we present another type of machining. What will the turner answer to the question of how life is going on ? : “Somehow it turns.” That’s it! In the modern world of CNC machining, it is not enough to just ‘somehow’ turn. The range of cutting tools is constantly expanding, materials and coatings allow higher cutting data to be set which enables to reduce time and increases productivity. Selecting the correct cutting strategy improves tool life and component quality.
I will start with the basics that one should know as standard. In short – if the workpiece rotates and the tool moves we speak of turning. Remember that in the basic formula for the cutting speed (Drawing 1), there is the diameter of the workpiece, and the cutting force is a component of the main circumferential force Fc, the feed force Ff and the radial resistance force Fp (Drawing 2). Each turning task should be considered individually – when preparing a task, I mean types of turning such as planning, rough turning, finishing turning also known as profile turning, grooving, parting off, thread turning, rough boring or finishing boring. There are more turning divisions in the literature but I have presented the most useful one.
Drawing 1. Cutting data in turning [source: “Machining Handbook” SandvikCoromant]
Drawing 2. The distribution of cutting forces in turning [source: “Machining” K. Jemielniak]
In software terms, turning belongs to quite friendly types of machining because we operate mainly with the X and Z axes. There are also several rules related to the preparation of production whether we talk about turning, milling or even grinding. First, the exact definition of the workpiece – its shape, geometrical requirements, tolerance, dimensions, surface roughness. Will we just turn? Will we bore? Do we consider a stable short detail or a long and thin-walled one? What rays should be outlined? All the answers have a direct impact on the preparation of the process and the selection of appropriate tools.
Another thing, of course, is the material of the workpiece. What insert will be used and what cutting parameters will be choosen is strictly related to the material we are going to process. During one of the e-learning trainings on the
Sandvik Coromant platform (I highly recommend it!), I came across a detailed overview of the chip appearance depending on the material (Drawing 3). Therefore, when turning titanium we will more confidently focus on round inserts, a small depth of cutting and the right strategy to avoid notch and while turning aluminum, a sharp positive insert and high cutting speeds will be the basis.
Drawing 3. The nature of the chips depends on the material of the workpiece [source: e-learning https://www.sandvik.coromant.com/pl-pl/services/education/pages/e-learning.aspx]
What about the shape of the insert? There is a certain logical rule that the greater the point angle the greater the strength. Therefore, round, square, rhombic C and trigonal inserts will be stronger and better for example in rough machining rather than triangular, rhombic D and rhombic V. Apart from the tasks the inserts are to perform, it is worth checking, for example, the number of cutting edges that a given insert has.
The last issue I am going to mention is solving common machining problems. Which parameter affects the blade durability the most? Cutting speed. Too low vc causes built-up edge and is simply uneconomical while too high vc will contribute to poor quality of the processed detail. Chip breaking problem? It is worth changing the cutting depth , experimenting with the feed and if the problem still occurs, changing the insert to a different geometry may solve the problem. Vibrations? Very poor surface quality when turning long, slender shafts? A lot of modern machines have an additional anti-vibration function. It works by continuous change of the rotation as a function of time. I attach the link to the video that illustrates the problem:
https://www.youtube.com/watch?v=dXR2wDDFFm4
In case of Hass machines it is the SSV function, i.e. Spindle Speed Variation, in DMG machines, for example, you should look for the Alternating Speed function and in Okuma – Harmonic Spindle Speed Control. Each works on the same principle.
Turning is undoubtedly a vast topic, today’s article is only a substitute that may contribute to the beginning of searching for knowledge in this area.
Natalia Matuszczyk
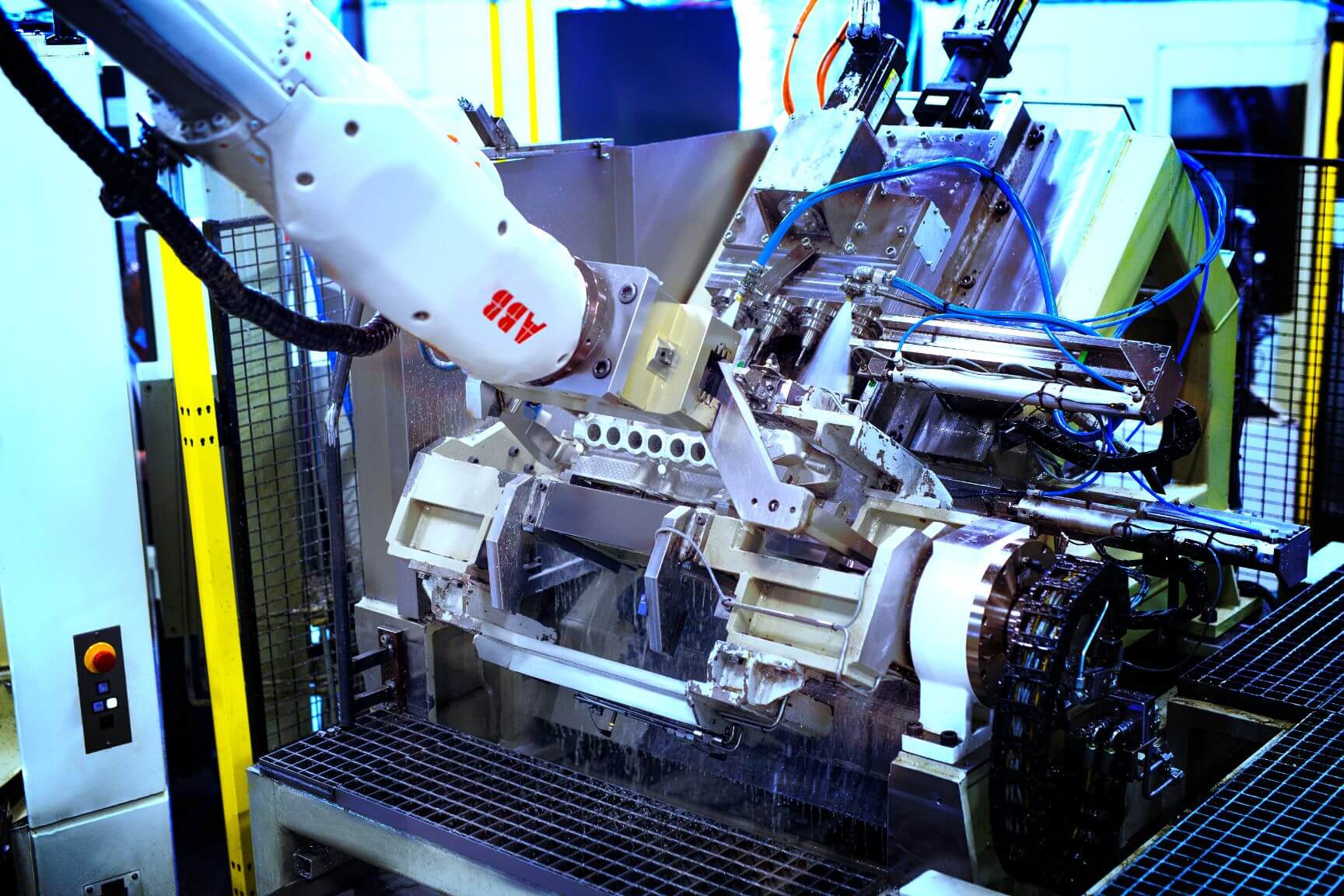